Aby usprawnić obsługę procesową magazynu w tych obszarach kierownik działu utrzymania ruchu powinien odpowiedzieć sobie na kilka kluczowych pytań:
- Jakie są typowe problemy magazynów technicznych?
- Jak ułatwić monitorowanie rozchodów części zamiennych oraz inwentaryzacje magazynów?
- Jak zautomatyzować procesy zamówień oraz przyjęć?
- Jak wyciągać wnioski w celu optymalizacji i zmniejszenia kosztów?
W tym artykule spróbujemy odpowiedzieć na te pytania oraz podamy przykłady jak system CMMS może usprawnić zarządzanie magazynem technicznym części zamiennych.
Problemy związane z gospodarką częściami zamiennymi z perspektywy utrzymania ruchu.
Utrzymanie ruchu odpowiada za wiele procesów niezbędnych dla poprawnego działania zakładu oraz zapewnienia jak najwyższej dostępności technicznej maszyn i urządzeń. Jednym z nich jest zarządzanie magazynem technicznym, które niesie ze sobą wiele wyzwań.
Zaczynając od początku: wiele firm boryka się z problemem niedokładnego lub całkowitego braku monitorowania rozchodów części zamiennych, przez co pracownicy nie mają ich wtedy, kiedy realnie są im potrzebne np. w sytuacji awarii kluczowej dla funkcjonowania zakładu maszyny. Takie sytuacje powodują przedłużanie się przestojów i generują znaczne straty finansowe
Problemy z dostępnością części pojawiają się również ze względu na niewłaściwe monitorowanie stanów minimalnych czy choćby ich brak, co może prowadzić do analogicznych, jak w przypadku rozchodów części zamiennych, problemów. Brak odpowiednich stanów minimalnych może m.in. wiązać się z koniecznością złożenia pilnego zamówienia u dostawcy, co często oznacza dużo wyższe koszty niż przewidywane. o ile nie ma ustalonych stanów minimalnych, dochodzi do sytuacji, w której dane części się skończyły, a my o tym nie wiemy.
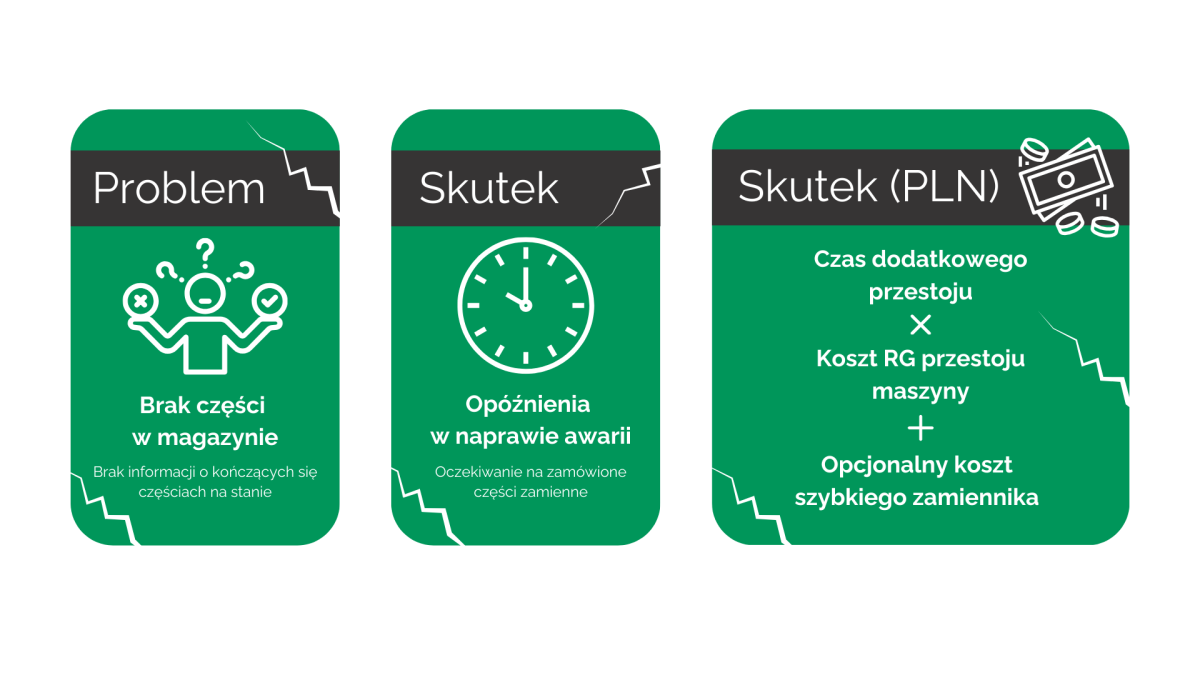
Brak widocznej lokalizacji części w magazynie może doprowadzić do szeregu problemów związanych z czasem przedłużającego się poszukiwania ich gdy nagle okazują się bardzo potrzebne. Wiąże się to oczywiście z wydłużeniem czasu trwania awarii i kosztów z nimi związanych. W skrajnych przypadkach pracownicy z powodu dezorientacji, zgłaszają zapotrzebowanie na części, które są w magazynie, ale nie mogą ich znaleźć. To prowadzi do niepotrzebnych zamówień oraz marnotrawstwa kluczowych zasobów.
Brak kategoryzacji części, czy to w kontekście szybkości ich rotowania, czy też krytyczności, utrudnia podejmowanie decyzji zakupowych w wyniku niekompletnych i nieprecyzyjnych informacji.
Brak jasnych wytycznych dotyczących procesu zamawiania może powodować problemy związane z przedłużającymi się dostawami, niedokładnymi przyjęciami a choćby brakiem przejrzystości finansowej, w wyniku niezorganizowanego i chaotycznego procesu.
Bez informacji o rozchodach, trudno jest dokonać szczegółowej analizy kosztów – może to utrudniać planowanie budżetu i podejmowanie decyzji finansowych. Bez danych o tym, jaki procent kosztów stanowią części, trudno jest zidentyfikować obszary, które mogą być optymalizowane w celu oszczędności i planowania budżetu.
Jak systemy CMMS pomagają w rozwiązywaniu problemów magazynów technicznych?
Systemy CMMS oferują standardy działań prewencyjnych oraz procedury obsługi awarii. Umożliwiają też generowanie niezbędnej dokumentacji. Jednym z takich standardowych procedur jest rejestracja wykorzystania części zamiennych. Najczęściej jest ona powiązana z samym procesem wykonywania zdarzeń oraz wymaga rejestracji tego, jaka część została wykorzystana. Można jej dokonywać na przykład przez wykorzystanie kodów QR lub kodów kreskowych.
Dzięki temu wszystkie procedury są ustandaryzowane, nie potrzeba dodatkowej dokumentacji w formie pisemnej, a wszelkie informacje o zużyciu oraz zmianach stanów są dostępne w historii.
Przykład: Podczas działań dążących do rozwiązania awarii, system pyta, czy pracownik potrzebuje jakichś części. Po rozpoznaniu maszyny, której dotyczyło dane zdarzenie, system podpowiada przykładowe części. Pracownik udaje się do magazynu, następnie skanuje kod QR umieszczony na danej części lub półce oraz zapisuje, ile części pobrał. Automatycznie zliczana jest pobrana z magazynu ilość części, następnie generowana jest dokumentacja, zdjęcia oraz naliczane są koszty konkretnej maszyny lub MPK.
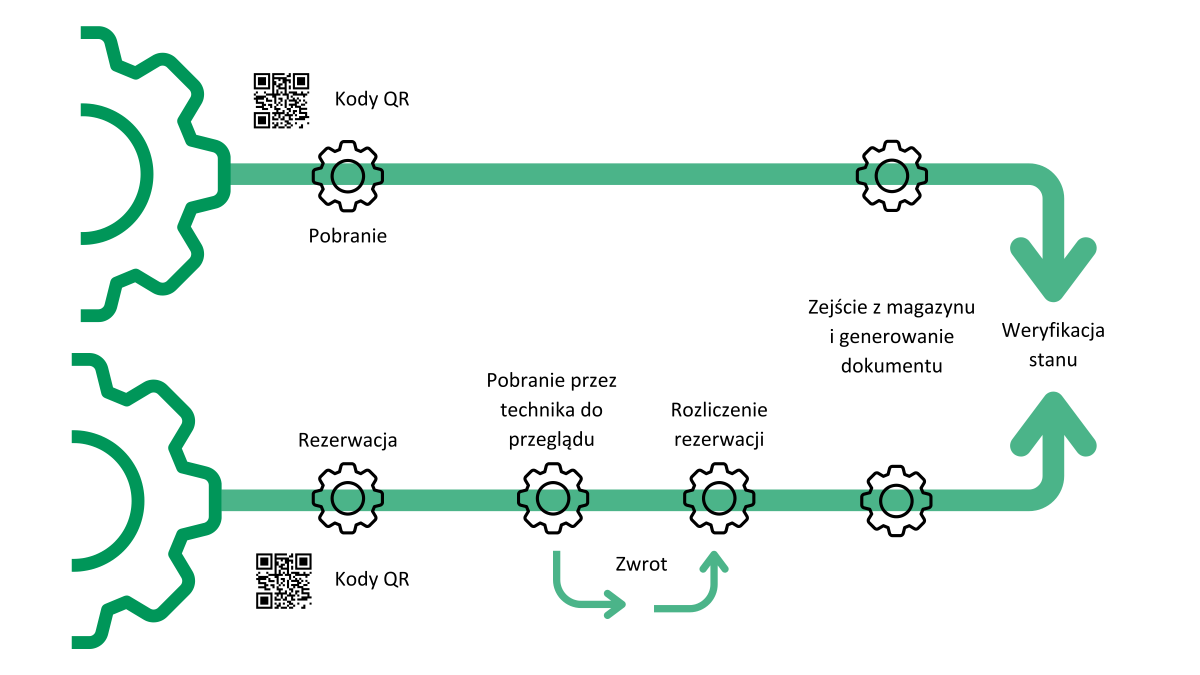
Systemy zapisują wiele informacji niezbędnych do poprawnego wsparcia magazynierów, ale też techników. Podstawowe informacje dotyczą dostępności, kategoryzacji części, lokalizacji fizycznej w magazynie, maszyn, do których części pasują oraz niezbędnych stanów zamówień. Przy osiągnięciu stanów minimalnych najczęściej o takiej sytuacji informowani są kierownicy oraz osoby odpowiedzialne za magazyny.
Dzięki temu technicy mają dostęp do niezbędnych informacji i nie tracą czasu w poszukiwanie części w magazynie. Dodatkowo, dostępność części w magazynie jest na bieżąco monitorowana, a wszelkie braki wychwytywane są na bieżąco, co pozwala na odpowiednio wczesną reakcję.
Przykład: Technicy na bieżąco mają dostęp nie tylko do części zamiennych do konkretnych maszyn i innych obiektów, ale również podglądu stanów wszystkich części w magazynie. System po pobraniu automatycznie weryfikuje stany i warunkuje dalsze działania na ich podstawie (dotyczy to nie tylko stanów minimalnych, ale i maksymalnych). Może dodatkowo informować o zmianach w rezerwacjach części wynikających np. z planowanego remontu. W razie wykrycia potrzeby zakupu całkowicie nowej części, technicy mogą zgłosić zapotrzebowanie do działu zakupów wraz z niezbędnymi informacjami.
Systemy na podstawie wyżej wymienionych stanów potrafią automatycznie przypominać o niezbędnym zamówieniu oraz generować gotowe szablony maili do dostawców. istotną informacją jest możliwość śledzenia zamówienia oraz późniejszych możliwości przyjęcia dostawy do magazynu.
Dzięki temu wszystkie procesy magazynów technicznych są zapisywane, statusy zamówień są na bieżąco monitorowane, a sam dział UR ma wszystkie narzędzia w jednym rozwiązaniu.
Przykład: W momencie osiągnięcia minimalnego stanu zamówienia, systemy informują wybrane osoby i generują zamówienie do dostawcy, w oparciu o zarejestrowane dane. Po tym procesie pracownik otrzymuje potwierdzenie wysłania zamówienia przez przełożonego. Później rejestrowane jest zamówienie wraz z przewidywanym terminem dostawy. Ostatnim krokiem jest przyjęcie części do magazynu oraz zasilenie stanów.
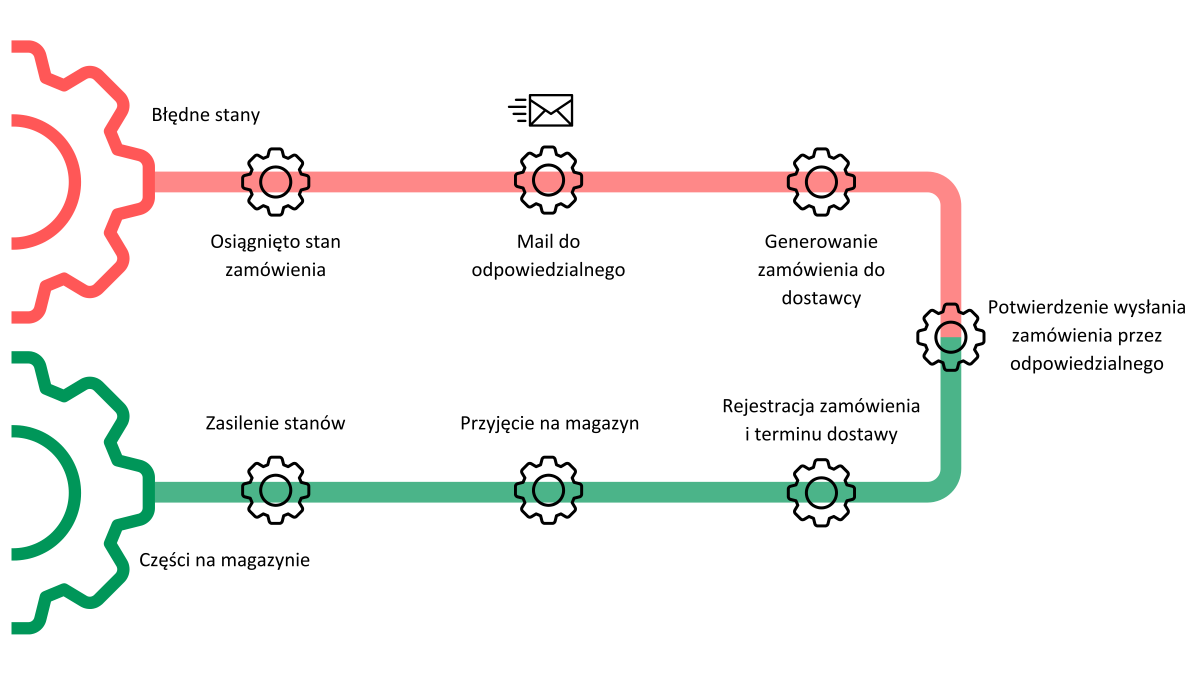
Możliwości integracji CMMS z systemami ERP
Często poruszanym tematem przy omawianiu obsługi magazynów technicznych w systemach CMMS jest możliwość integracji z obecnymi w organizacji programami ERP (Enterprise Resource Planning). Integracja może być rozumiana jako wyrównanie danych między jednym a drugim systemem lub rozpoczęcie procesu w jednym systemie i przekazanie go do drugiego.
Skutki integracji z ERP obejmują optymalizacje kosztowe, eliminację powielania procesów oraz zapewnienie spójności danych w obu systemach. Systemy CMMS umożliwiają dokładne rozdzielenie kosztów na komponenty obiektów technicznych, co jest zbędne z punktu widzenia systemu ERP.
Innym ważnym aspektem jest to, iż dział techniczny pracuje głównie na systemie CMMS. Takie rozwiązanie umożliwia automatyzację procesów poprzez rozdzielenie działań między pracownikami, eliminując „przezbrojenia” pomiędzy dwoma systemami.
Przykład: Pracownik działu utrzymania ruchu pobiera części zamienne podczas awarii przez aplikację mobilną. System CMMS wysyła informacje o zdjęciu części i pomniejszeniu dotychczasowego stanu w systemie ERP. Zapisywana jest wtedy informacja: w jakim celu i ile części zostało pobranych. W przypadku zamówienia wszystkie ważne dane zapisywane są w systemie CMMS, a do systemu ERP przesyłane jest prawie gotowe zamówienie. Wymaga jedynie biznesowego przypisania przez kierowników lub dział zakupów.
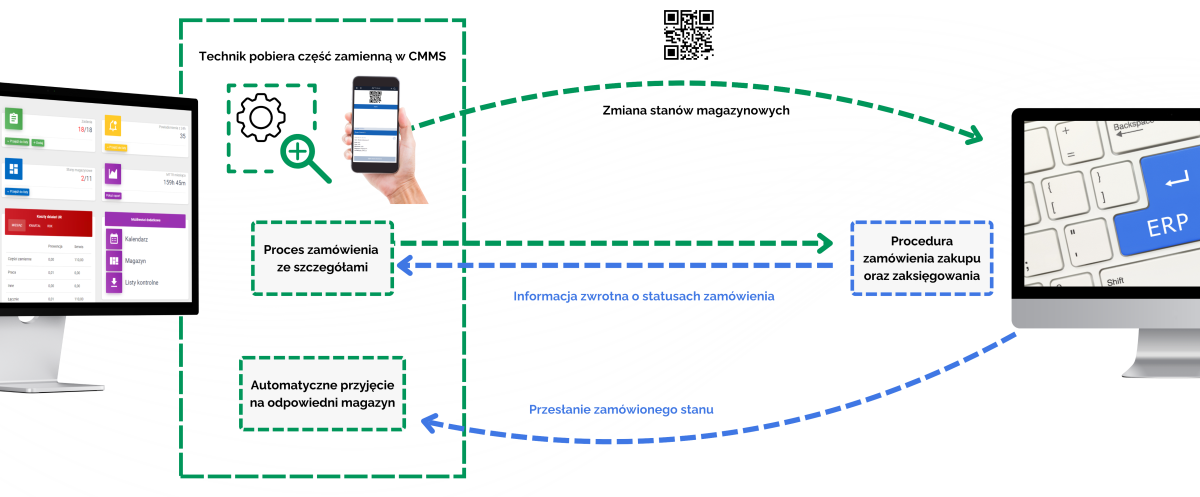
Możliwości optymalizacji na podstawie danych w systemie CMMS
Jednym z przykładów takich optymalizacji są raporty zużycia oparte na Analizie Pareto, które pozwalają identyfikować najczęściej używane części zamienne i podejmować odpowiednie działania zarządcze. Dzięki temu, firmy mogą skupić swoje wysiłki na zarządzaniu kluczowymi częściami, co może prowadzić do znacznych oszczędności.
Modyfikacja stanów na podstawie historii: System CMMS jest w stanie monitorować zużycie części zasobów w określonym czasie, co umożliwia analizę trendów i optymalizację stanów magazynowych. Na przykład, o ile określone części są często zużywane w danym okresie, system może sugerować zwiększenie zapasów na ten czas.
Przewidywanie zapotrzebowania w kontekście analizy prewencyjnej: System CMMS może wspierać w planowaniu przeglądów i wymiany części. Może on generować automatyczne przypomnienia o konieczności zakupu części na podstawie historii zużycia i harmonogramu przeglądów. Ponadto, o ile po przeglądzie wystąpi awaria wymagająca użycia określonej części (np. UHT), system postara się przewidzieć, iż taka sytuacja może się powtórzyć i zasugeruje zamówienie dodatkowych części.
Planowanie budżetów na części: System CMMS jest w stanie monitorować wykorzystanie części, co umożliwia precyzyjne planowanie budżetu. Można uwzględnić czynniki takie jak inflacja, eksploatacja parku maszynowego i jego planowane powiększenie.
Optymalizacja procesu zamówienia na podstawie historii współpracy z dostawcą: o ile dostawca ma długi czas dostawy, system CMMS może wspierać w planowaniu zamówień tak, aby były one składane odpowiednio wcześnie, zanim stan magazynowy spadnie poniżej minimum. System może przewidywać, kiedy to nastąpi, na podstawie historycznego zużycia części w konkretnych okresach.
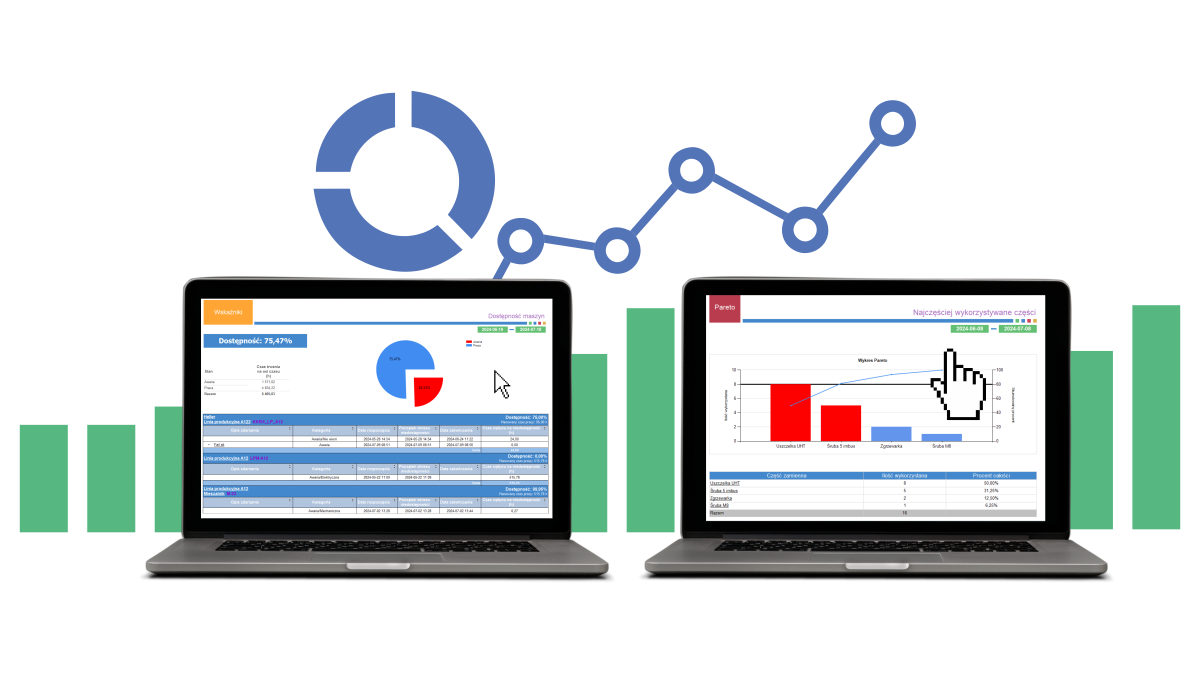
Podsumowując
W konkurencyjnym środowisku przemysłowym, efektywne zarządzanie magazynem technicznym i częściami zamiennymi jest kluczowym elementem skutecznego utrzymania ruchu. Dzięki systemom CMMS, firmy mogą zoptymalizować procesy związane z gospodarką częściami, minimalizując przestoje maszyn i zwiększając wydajność produkcji. Jednocześnie, integracja CMMS z systemami ERP oraz wykorzystanie zaawansowanych funkcji analizy danych pozwalają na jeszcze efektywniejsze zarządzanie zasobami i redukcję kosztów operacyjnych.
Poza tym systemy oferują również inne rozbudowane funkcje, jak inwentaryzacje dzięki urządzeń mobilnych, integracje z innymi systemami magazynowymi czy automatyczne indeksowanie i predykcje zużycia części dla konkretnych awarii. Podstawą jednak jest początkowe określenie standardów i dostosowanie systemu CMMS do potrzeb organizacji.