W ciągu ostatnich lat lista wyzwań, z jakimi mierzą się firmy produkcyjne zdaje się nieustannie wydłużać. Rosną ceny energii, zwłaszcza w przemyśle energochłonnym, inflacja podnosi oczekiwania płacowe, a także koszty związane z obsługą długów przedsiębiorstw. Braki surowców i komponentów, oraz zerwane czy niepewne łańcuchy dostaw sprawiają, iż zaplanowanie i zagwarantowanie czasu dostaw staje się niesłychanie trudne. To wpływa na spadek zamówień i coraz trudniejsze relacje z klientami.
Zarządzanie łańcuchem wartości jest poddane dużej próbie. Niepewne przychody i zamówienia oraz rosnące koszty sprawiają, iż margines zysku brutto się zmniejsza. Odpowiedzią na te wyzwania może być wprowadzenie tzw. cyfrowego redundantnego łańcucha wartości, czyli takiego, którym można zarządzać z wykorzystaniem systemów informatycznych, takich jak cyfrowy bliźniak, a więc wirtualny model całego łańcucha wartości.
Rozwiązania takie pozwalają na bieżąco mierzyć zapotrzebowanie na surowce i półprodukty, wyznaczać optymalne ceny produktów i gwałtownie przerzucać się na alternatywne źródła komponentów, a tym samym zachować ciągłość produkcyjną i biznesową oraz dobre relacje z partnerami i klientami końcowymi. Sformułowanie „redundantny”, w tym kontekście, oznacza „nadmiarowy”, czyli gwarantujący zapas. W środowisku produkcyjnym chodzi o zapasowe źródła surowców i komponentów.
Ponieważ świat jest połączony jak nigdy przedtem i dostawcy (producenci komponentów) są zlokalizowani w różnych jego częściach, a trafiają tam w poszukiwaniu niższych kosztów produkcji, redundantny cyfrowy łańcuch wartości staje się rozwiązaniem coraz bardziej powszechnym. W szczególności widać to w branżach produkcji samochodów (automotive), produkcji elektroniki, ale też np. w produkcji rowerów. Nowy trend, w mniejszym lub większym stopniu, dotyczy jednak wszystkich branż i sektorów.
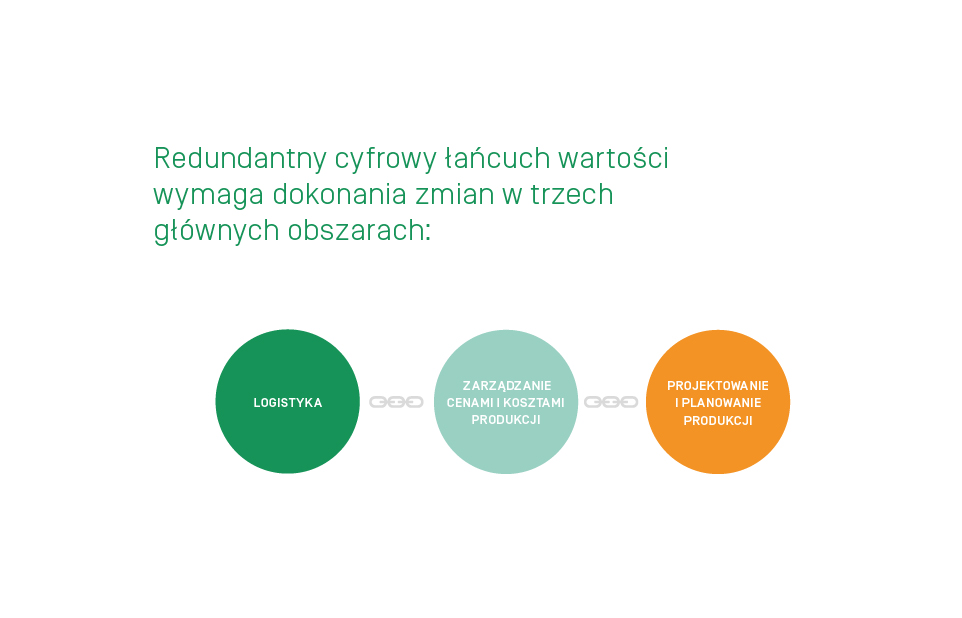
Skuteczną ochronę przed zmiennym otoczeniem biznesowym gwarantuje tylko zintegrowanie działań we wszystkich trzech obszarach. Co konkretnie, w każdym z nich warto zmienić?
1. Oprzyj logistykę na informacji
Zadbaj o cyfrową integrację przepływu informacji w systemach dostawców i poddostawców. Chodzi o to, by mieć stały wgląd w ich zasoby, z dużym wyprzedzeniem przewidywać pojawienie się niedoborów i móc reagować proaktywnie na te trendy, robiąc zapasy. W integracji informacji pomogą szyny danych i rozwiązania chmurowe. W następnym kroku zadbaj o dywersyfikację źródeł dostaw. W tym celu nawiąż relacje z wieloma dostawcami alternatywnych półproduktów, komponentów czy surowców, aby móc płynnie przejść od jednego dostawcy do drugiego, gdy pojawią się problemy. Następnie zadbaj o dynamiczne zarządzanie bieżącymi i przyszłymi kosztami oraz harmonogramami transportu, by móc w czasie rzeczywistym reagować na zmiany sytuacji w otoczeniu firmy.
Ostatni element układanki to cyfrowa optymalizacja stanów magazynowych, obejmująca też utrzymanie zapasów, czyli uwzględniająca informacje pochodzące z systemów informatycznych firmy, od dostawców i otoczenia rynkowego. Dzięki temu można przygotować firmę na ryzyko przerwania dostaw.
PRZYKŁAD: Cyfrowy bliźniak, a więc wirtualna kopia łańcucha wartości, pozwala zebrać informacje z wyżej wymienionych systemów i zaplanować działania będące odpowiedzią na rozmaite scenariusze rynkowe w obszarze logistyki.
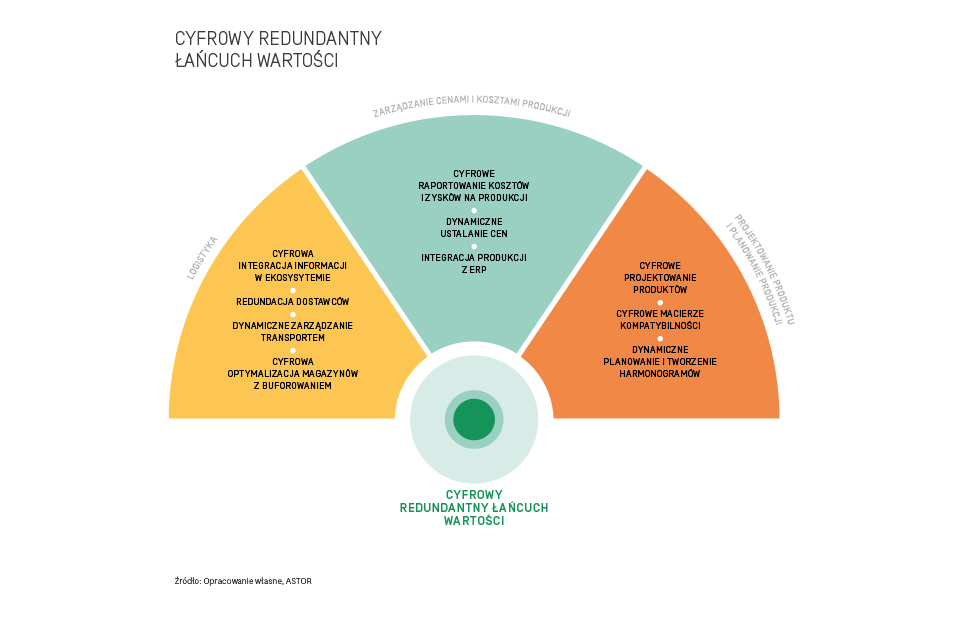
2. Wprowadź dynamiczne mechanizmy kontroli kosztów i ustalania cen
Wykorzystanie systemów informatycznych do stworzenia redundantnego łańcucha wartości pozwala budować dynamiczne mechanizmy ustalania cen, z uwzględnieniem aspektów logistycznych, realnych kosztów produkcji i prognoz zamówień.
Aby taki mechanizm stworzyć, firma musi mieć dostęp do realnych danych na temat kosztów produkcji i to takich, które generowane są automatycznie, w czasie rzeczywistym. Powinna też mieć strategię i politykę cenową, które można później powiązać z kosztami produkcji. Najbardziej zaawansowany scenariusz zakłada, iż projektowaniem cen zajmują się algorytmy sztucznej inteligencji. W scenariuszu bardziej bazowym należy zadbać o podstawowe kompetencje na styku operacji produkcyjnych i systemów biznesowych (ERP) oraz o cyfrowe raportowanie kosztów produkcji w czasie rzeczywistym – np. zysk wypracowany w czasie jednej zmiany, w czasie realizacji jednego zlecenia, czy w przeliczeniu na jeden produkt. Wykorzystanie tych danych i ich zautomatyzowanej analizy pozwoli na dynamiczne skorelowanie ceny z realnymi kosztami produkcji.
PRZYKŁAD: Cyfrowy bliźniak to rozwiązanie integrujące wszystkie te systemy, które w obszarze wirtualnym pozwala testować rozmaite scenariusze cenowe przy takich, a nie innych, rzeczywistych kosztach produkcji.
3. Cyfrowo optymalizuj projektowanie produktu i harmonogramowanie produkcji
W niepewnych czasach produkt powinien być projektowany z takich komponentów, które są w tej chwili dostępne, ale też takich, które najprawdopodobniej będą dostępne w najbliższej przyszłości. Aby tak było, w systemach informatycznych należy stworzyć tzw. macierze kompatybilności, pozwalające na budowanie w sposób dynamiczny list materiałowych dla produktów na bazie dostępnych komponentów. Takie narzędzie znacząco przyspiesza proces projektowania i ułatwia proces wyboru adekwatnych komponentów.
Jeśli zaś chodzi o harmonogramowanie produkcji, należy zadbać o wprowadzenie dynamicznego planowania krótkoterminowego, czyli system pozwalający na bieżąco dostosowywać produkcję do zmieniających się terminów i zakresów dostaw komponentów przy maksymalnym możliwym i najbardziej efektywnym wykorzystaniu mocy produkcyjnych. Pozwoli to na dynamiczne skorelowanie ceny z realnymi kosztami produkcji.
PRZYKŁAD: Integracja tych narzędzi w ramach wirtualnego modelu (cyfrowego bliźniaka) pozwala zaplanować i przetestować rozmaite scenariusze, a docelowo zapewnić przewidywalne terminy zleceń produkcyjnych.
Dowiedz się więcej
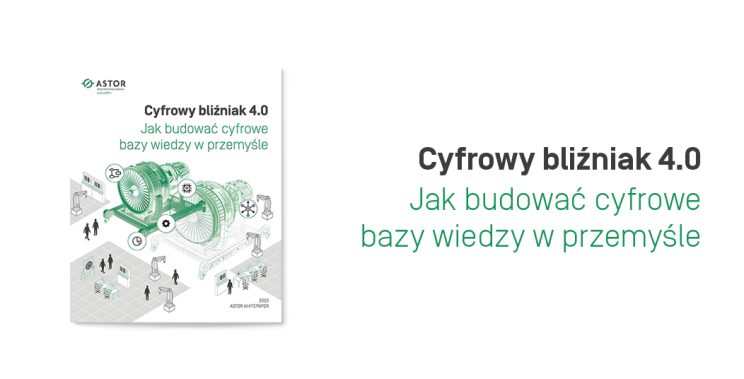
Dowiedz się więcej o cyfrowym bliźniaku w nowej publikacji „Cyfrowy bliźniak 4.0. Jak budować cyfrowe bazy wiedzy w przemyśle.„