ADvanced MAnufacturing (ADMA). Pierwszy krok do sukcesu
Metodologia badania ADMA została stworzona przez Komisję Europejską w 2018 roku w celu ułatwienia przedsiębiorstwom wdrażania nowych technologii oraz przyjmowania strategii innowacyjności. Per saldo, pomaga także firmom produkcyjnym otrzymać status Fabryki Przyszłości (ang. Factory of the Future).
Wyniki badania dojrzałości cyfrowej ADMA wskazują organizacjom pożądane ścieżki rozwoju. Określają, jak dokonywać transformacji fabryk, by stawały się innowacyjne, konkurencyjne i działały na rzecz zrównoważonego rozwoju.
Firmy produkcyjne, pragnące poznać poziom swojego zaawansowania cyfrowego, nie powinny jednak działać same. Gdy są już gotowe na wykorzystanie metody ADMA, powinny zwrócić się o pomoc osób posiadających kompetencje do przeprowadzania audytów dojrzałości cyfrowej przedsiębiorstwa, czyli do konsultantów ADMA. Do ich zadań należy przede wszystkim wsparcie w zaplanowaniu oraz przebiegu całego procesu, a tym samym wypracowanie obiektywnej oceny dojrzałości cyfrowej zakładu oraz wskazanie obszarów i możliwych rozwiązań, które doprowadzą przedsiębiorstwo do statusu Fabryki Przyszłości. Firmy, które upoważnione są do przeprowadzania badania ADMA nazywane są organizacjami wspierającymi. W Polsce są to m.in. ASTOR i Krakowski Park Technologiczny.
Badanie ADMA składa się z trzech głównych etapów, którymi są skan ADMA, plan transformacji oraz plan implementacji.
I. Skan ADMA
W pierwszej kolejności dokonywana jest samoocena przedsiębiorstwa, czyli weryfikacja, w jaki sposób pracownicy z różnych działów oceniają poszczególne obszary. Do jej przeprowadzenia służy ankieta, która zawiera 51 pytań dotyczących 7 obszarów transformacji (obszary te omawiamy w sekcji Plan Implementacji). Ważnym elementem wspierającym wypracowanie obiektywnej oceny jest wypełnienie ankiet w sposób niezależny przez min. 3 pracowników badanego przedsiębiorstwa.
Kolejnym krokiem jest zewnętrzny audyt zakładu przeprowadzany przez konsultantów ADMA. Podczas wizyty w firmie specjaliści oceniają stan obecny przedsiębiorstwa oraz przeprowadzają dyskusję w oparciu o ich spostrzeżenia podczas audytu oraz w oparciu o raport wstępny przygotowany na podstawie ankiety. Pozwala to na wypracowanie obiektywnej oceny firmy oraz wskazanie obszarów, które powinny być rozwijane.
II. Plan transformacji
Kolejnym etapem jest zbudowanie planu transformacji, czyli listy inicjatyw, wykorzystujących technologie Przemysłu 4.0, wraz ze zdefiniowanymi celami biznesowymi oraz miernikami. Inicjatywom należy nadać priorytety i określić ich wpływ na biznes. Priorytetowe inicjatywy wpisujemy w konkretny kontekst przedsiębiorstwa z uwzględnieniem spodziewanego zaangażowania ludzi, procesów, na które transformacja będzie miała wpływ oraz technologii, które planujemy wykorzystać.
III. Plan implementacji
Plan implementacji jest szczegółowym harmonogramem wdrożenia wybranych inicjatyw. W zależności od tego, co pokaże skan ADMA, firma wybiera ścieżkę transformacji. Podejmuje decyzję na temat tego, który z siedmiu głównych obszarów transformacji wymaga najpilniejszego działania.
Realizacja planu implementacji wymaga wyznaczenia odpowiedniego zespołu specjalistów oraz opracowania mapy drogowej, wskazującej konkretne zadania dla każdej z osób, rozłożone w czasie.
Metodologia ADMA definiuje 5 stopni dojrzałości cyfrowej:
- Bardzo podstawowy poziom cyfryzacji.
- Poziom podstawowy cyfryzacji, połowa drogi w kierunku Fabryki Przyszłości.
- Poziom średniozaawansowany.
- Poziom Fabryki Przyszłości.
- Poziom doskonalącej się Fabryki Przyszłości.
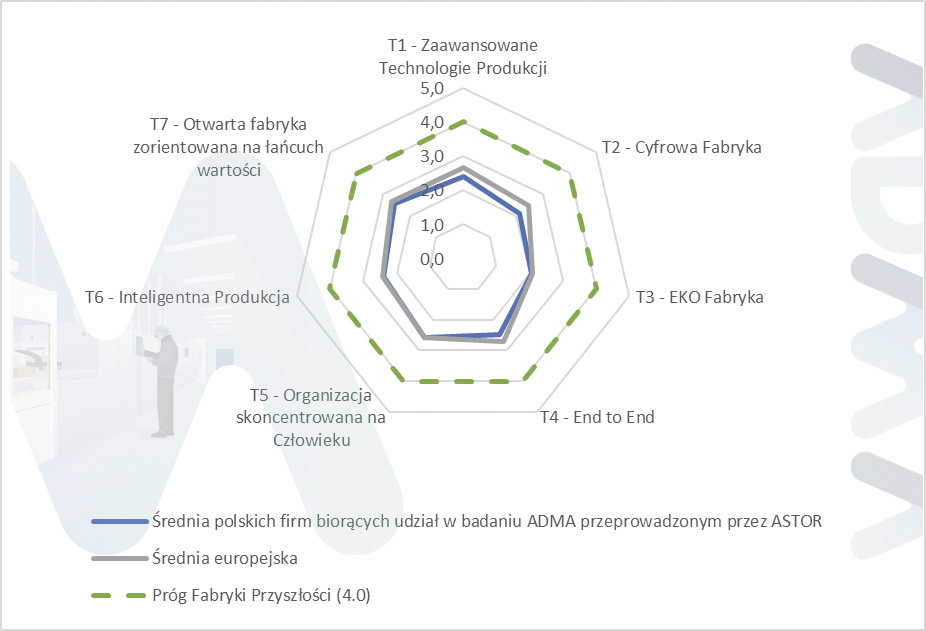
W jakim stopniu polskie przedsiębiorstwa produkcyjne korzystają z cyfrowej transformacji?
W badaniach przeprowadzonych przez ASTOR z wykorzystaniem metodologii ADMA wzięło udział 16 firm produkcyjnych z Polski.
Na powyższym wykresie zaprezentowano wyniki polskich przedsiębiorstw na tle średniej dla wszystkich firm europejskich, które wzięły udział w badaniu.
Można zauważyć, iż poziom zaawansowania technologicznego polskich przedsiębiorstw nie odstaje od średniej europejskiej. Najwyraźniejsza różnica zauważalna jest w obszarze 2 „Budowa cyfrowej fabryki”. Wynik polskich przedsiębiorstw jest w nim gorszy.
Zarówno europejska, jak i polska średnia nie przekraczają progu Fabryki Przyszłości. Warto jednak zauważyć, iż wyniki wskazują, iż w zakładach produkcyjnych cyfryzacja została opanowana na podstawowym poziomie. Oznacza to, iż firmy zastosowały już pewne rozwiązania w celu ulepszenia swojego działania, takie jak np. robotyzacja wybranych stanowisk, wdrożenie systemów klasy SCADA, ERP itp. Dodatkowo, sam udział w badaniu ADMA udowadnia, iż firmy czują potrzebę zmian oraz rozumieją korzyści wynikające z cyfrowej transformacji.
Siedem obszarów transformacji według metodologii ADMA:
Obszar 1: Wdrażanie zaawansowanych technologii produkcji
Koncentracja jest na uzupełnieniu parku maszynowego, czyli zaplanowaniu, jakie maszyny, roboty, urządzenia i przestrzeń powinny docelowo być wykorzystywane w działaniu zakładu.
Obszar 2: Budowa cyfrowej fabryki
Nacisk na implementację technologii cyfrowych, uspójnienie sposobu zbierania i wykorzystywania danych oraz integrację systemów.
Obszar 3: Tworzenie EKO fabryki
Podjęcie działań mających na celu ograniczenie negatywnego wpływu przedsiębiorstwa na środowisko.
Obszar 4: Organizacja działań inżynierskich z myślą o kliencie końcowym (End-to-end)
Koncentracja na ofercie wartości: personalizacja, wyjątkowe usługi i produkty, wsparcie techniczne itp.
Obszar 5: Tworzenie organizacji skoncentrowanej na człowieku
Większy nacisk na dobrostan pracowników. Ich rozwój przyczynia się do dobrego samopoczucia, wysokiego poczucia własnej wartości a per saldo do rozwoju firmy.
Obszar 6: Wdrażanie rozwiązań inteligentnej produkcji
Poprawa komunikacji ludzie – maszyny i urządzenia – systemy.
Obszar 7: Otwieranie fabryki na potrzeby interesariuszy łańcucha wartości
Lepsze zrozumienie i dążenie do zaspokojenia potrzeb środowiska wewnętrznego i zewnętrznego, tj. klientów, dostawców itp.
Cyfrowa fabryka. Priorytetowy obszar rozwoju polskich przedsiębiorstw
Zdolność budowania cyfrowych fabryk jest więc tym obszarem, który w przypadku polskich przedsiębiorstw produkcyjnych pozostawia najwięcej do życzenia i wymaga największej pracy. Czym jednak cyfrowa fabryka jest konkretnie?
Zgodnie z nomenklaturą ADMA, cyfrowa fabryka wykorzystuje technologię cyfrową do tworzenia, przekształcania i rozwoju produktów, systemów i usług. Gwarantuje dokładność danych w każdym momencie, tworząc SSOT (pojedyncze źródło wiedzy, ang. Single Source of Truth). Oznacza to, iż poszczególne informacje wprowadzane są do systemu tylko raz, a wszystkie podsystemy pobierają je automatycznie. Ponadto, Fabryka Przyszłości wspiera pracowników poprzez cyfrowe i zintegrowane procesy. Zintegrowane sterowanie przepływem danych cyfrowych pozwala prowadzić rozmaite symulacje, czyli testowanie rozmaitych scenariuszy przed rzeczywistym wdrożeniem produktu czy procesu.
Warunkiem koniecznym do uzyskania powyżej opisanych efektów jest gromadzenie danych dotyczących procesów, poszczególnych maszyn czy linii produkcyjnych oraz integracja systemów.
Szczegółowa analiza działań, które można wykonać, aby usprawnić obszar cyfrowej fabryki, skupia się na dwóch filarach: infrastrukturze, która jest otwarta na komunikację oraz na możliwościach cyfrowych przedsiębiorstwa.
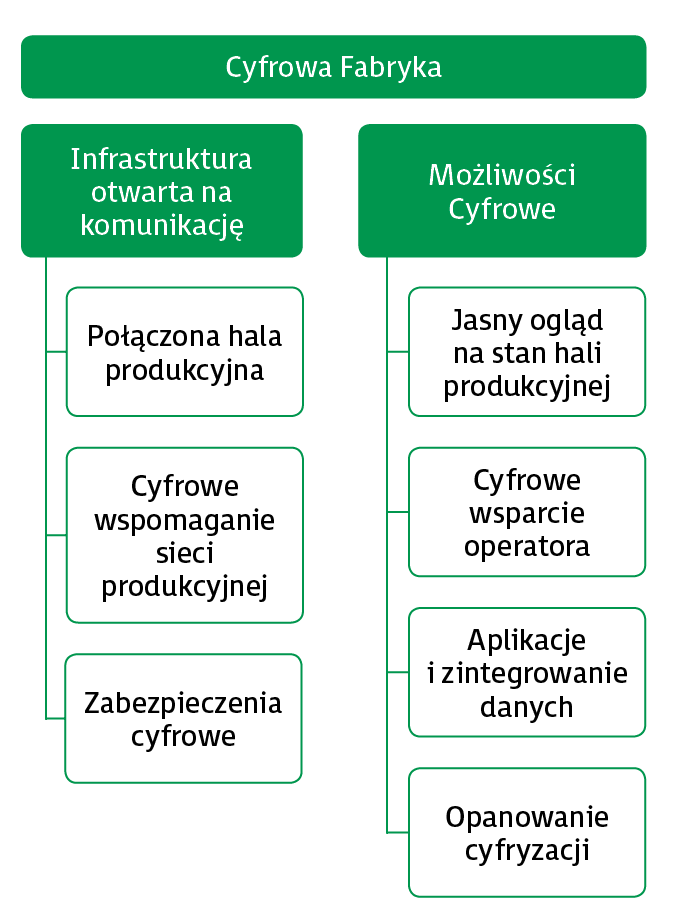
Jak skutecznie tworzyć cyfrowe fabryki?
Pierwszym stopniem poprawy efektywności na etapie budowania cyfrowej fabryki jest wytypowanie obszaru, który warto poddać transformacji. Metodologia ADMA jest tu szczególnie pomocna. Kiedy wiadomo już, jaki to obszar, niezwykle ważnym wyzwaniem staje się wybór konkretnego rozwiązania, a następnie jego implementacja. Oto przegląd technologii, które w sposób najbardziej efektywny pozwalają tworzyć cyfrowe fabryki:
Hala produkcyjna, w której poszczególne systemy są ze sobą połączone
Podobnie jak w relacjach międzyludzkich, komunikacja ma ogromne znaczenie w firmach produkcyjnych. Hala produkcyjna, której poszczególne komponenty są ze sobą połączone, taką komunikację zapewnia. Pozwala gromadzić dane na temat procesów, poszczególnych maszyn i niezbędnego osprzętu. Dzięki temu ułatwia zapewnienie ciągłości i jakości produkcji. Dodatkowo pozwala integrować te dane z inteligentnymi systemami. Im więcej informacji, tym lepiej można analizować bieżącą sytuację i efektywniej reagować na zdarzenia.
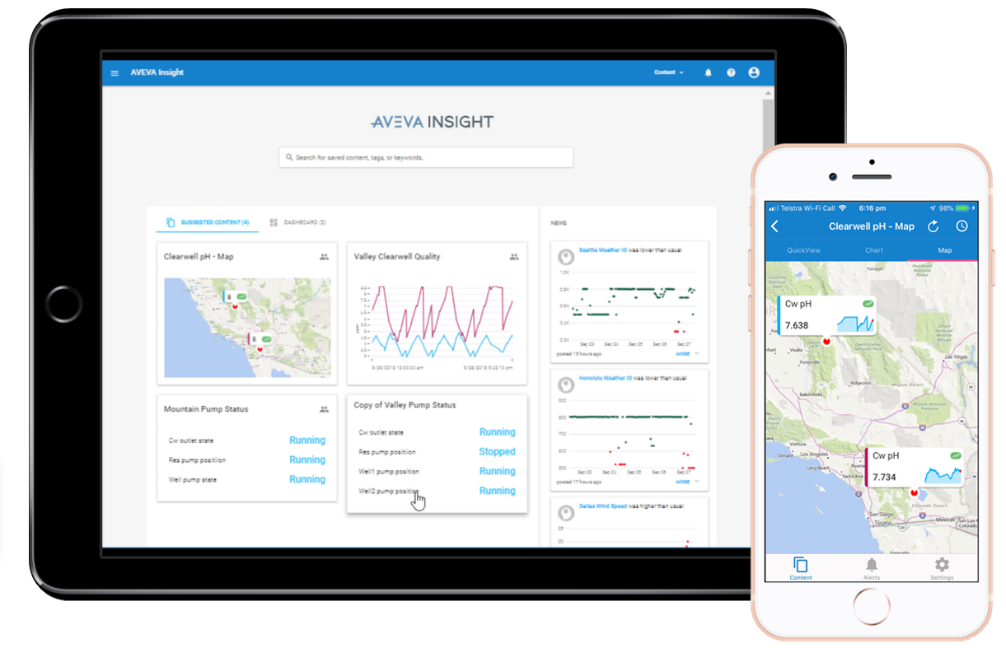
Niezależnie od tego, czy chcemy gromadzić dane z poszczególnych maszyn, czy całych fabryk, oprócz narzędzi do rejestracji informacji dot. produkcji, potrzebujemy miejsca, w którym możemy takie dane zbierać, by mieć do nich łatwy dostęp. Przemysłowe bazy danych klasy Historian umożliwiają gromadzenie danych historycznych oraz bieżących z różnych instalacji, np. systemów sterowania PLC, urządzeń oraz liczników, systemów informatycznych klasy HMI/SCADA, MES, ERP itp. Dane historyczne ułatwiają planowanie i harmonogramowanie, obserwację trendów, a choćby przewidywanie przyszłości poprzez wykorzystanie sztucznej inteligencji i analizy predykcyjnej. Predykcje mogą dotyczyć na przykład zużycia mediów. Pozwalają zakontraktować ich odpowiednią ilość, a tym samym nie przepłacać. Z kolei dane bieżące umożliwiają szybkie reagowanie na sytuacje kryzysowe, np. dzięki informacjom dotyczącym wystąpienia awarii.
Gromadzenie danych to pierwszy krok. Drugi to ich odpowiednia filtracja i klasyfikacja, pozwalająca z morza informacji (BigData) wyłowić te, które mają wpływ na najważniejsze procesy. Pomaga w tym wizualizacja danych i zaprezentowanie ich we właściwym kontekście. Dane przechowywane we właściwym systemie dają również możliwość automatycznego generowania przejrzystych i konkretnych raportów. Pomocą w wizualizacji oraz tworzeniu raportów są systemy klasy HMI/ SCADA czy control room. Mogą być to systemy małe (gromadzenie danych z maszyn i urządzeń), średnie (dane z linii produkcyjnych), duże (dane z całego zakładu), a choćby bardzo duże (gromadzenie danych z zakładów rozproszonych geograficznie).
Bardzo istotny i pomocny jest również mobilny dostęp do danych, który możliwy jest dzięki oprogramowaniu w chmurze lub rozwiązaniom hybrydowym.
Istotną rolę odgrywają szczegółowe dane, dotyczące realizacji produkcji, które mogą być gromadzone poprzez systemy klasy MES. System umożliwia ustandaryzowane i kompleksowe zarządzanie zleceniami produkcyjnymi, rejestrowanie genealogii, śledzenie produkcji, monitorowanie efektywności, przyczyniając się do zwiększania wydajności, podniesienia jakości produktów oraz redukcji kosztów jednostkowych produkcji.
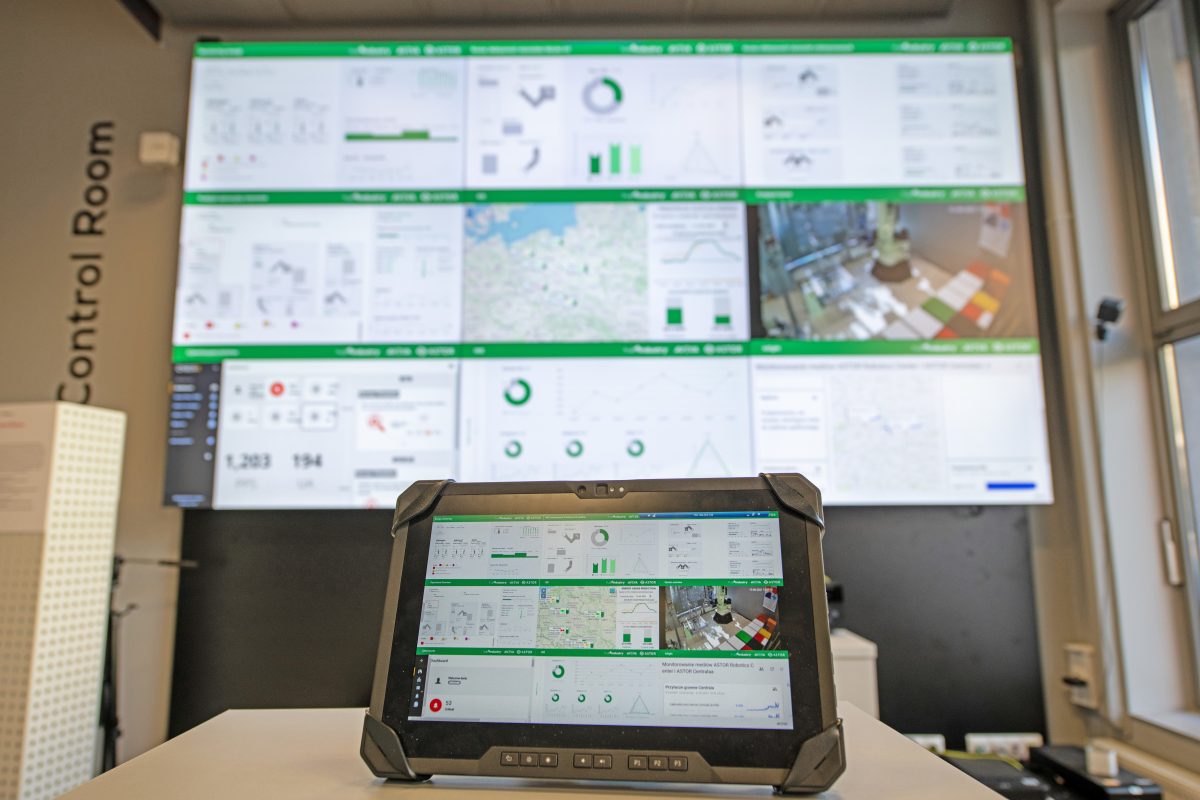
Cyfrowe wspomaganie sieci produkcyjnej oraz integracja z technologiami informacyjno-telekomunikacyjnymi
Komunikacja w obrębie hali produkcyjnej to pierwszy komponent, drugi to komunikacja w całym łańcuchu dostaw. Cyfrowe wspomaganie sieci produkcyjnej pozwala na automatyzację oraz cyfryzację procesów w łańcuchu dostaw, co przekłada się na przyspieszone składanie zamówień i sprawniejszą wymianę informacji z klientami, dostawcami i partnerami. Aby korzyści te mogły się pojawić, konieczna jest integracja cyfrowej fabryki z technologiami informacyjno-telekomunikacyjnymi.
Pracownicy produkcyjni często skarżą się na problem integracji systemów, które są zróżnicowane. Przedsiębiorstwa posiadają wiele systemów klasy SCADA, MES, ERP, WMS, APS, EDI itp., które często pochodzą od innych dostawców. Dlatego integracja tych systemów jest kluczowa do ulepszenia działania zakładu.
Zabezpieczenia cyfrowe
Cyfryzacja łączy się ze zwiększonym ryzykiem cyberataków, dlatego bezpieczeństwo sieci IT oraz OT powinno być priorytetem dla wszystkich z przedsiębiorstw. Zabezpieczenia cyfrowe w postaci systemu do wykrywania anomalii, włamań oraz rozpoznawania zagrożeń są niezbędne do prawidłowego i bezpiecznego funkcjonowania przedsiębiorstwa. Bardzo ważne jest nieustanne monitorowanie potencjalnych zagrożeń, pozwalające zabezpieczać poufne dane.
Przejrzysty wgląd w funkcjonowanie hali produkcyjnej
Zbieranie danych to jedno, odpowiednie ich wykorzystywanie to drugie. Uzyskanie przejrzystego wglądu w funkcjonowanie hali produkcyjnej powinno być wspierane przez system wspomagania decyzji klasy control room/ DSS. Umożliwia on pełną integrację, wizualizację, a tym samym analizę danych i trafne podejmowanie decyzji. Pozwala na stworzenie pojedynczego źródła wiedzy oraz analizę danych w czasie rzeczywistym, co umożliwia szybką reakcję na sytuacje kryzysowe, np. opóźnienia w dostawie surowców, awarie. Wspiera on podejmowanie trafnych decyzji biznesowych. Funkcje systemu control room mogą być wzbogacone dzięki wdrożeniu sztucznej inteligencji i uczenia maszynowego, które na podstawie historycznych i bieżących danych są w stanie wykrywać nadchodzące awarie czy przewidywać zużycie mediów.
Cyfrowe wsparcie operatorów i pracowników
Łatwy i mobilny dostęp do potrzebnej dokumentacji technicznej, instrukcji i innych potrzebnych informacji ułatwia pracę i zwiększa jej wydajność. Zapewniają go systemy cyfrowego wsparcia operatorów i pracowników. Dzięki nim operatorzy mają dostęp do wszystkich potrzebnych informacji i mogą dynamicznie z nimi pracować, np. zapewniając feedback, proponując zmiany. Główne elementy takich systemów to panele HMI, tablety czy okulary wirtualnej bądź rozszerzonej rzeczywistości. Może być to również cyfrowa platforma, która korzysta z chmury, aby łączyć pracowników z różnych stanowisk i zmian oraz usuwać luki w wiedzy i komunikacji. Takie rozwiązanie umożliwia natychmiastowy dostęp do wszystkich informacji, instrukcji, dokumentacji technicznych potrzebnych pracownikom. Daje możliwość komunikacji w czasie rzeczywistym, a tym samym szybsze działanie np. w sytuacji, gdy konieczna jest naprawa usterki.
Mamy plan i wskazówki. Co dalej?
Kolejnym wyzwaniem dla przedsiębiorstwa jest wybór rozwiązania oraz jego dostawcy. Wybór odpowiedniego partnera będzie znaczącym warunkiem sukcesu wdrożenia rozwiązania. adekwatny dostawca, oprócz dostarczenia konkretnej technologii czy produktu, powinien zapewnić odpowiednią wiedzę oraz wsparcie merytoryczno-techniczne w przygotowaniu oraz podczas wdrożenia, a choćby po jego realizacji. Niezwykle ważna jest również otwartość partnera na potrzeby konkretnego klienta. W obszarze cyfrowej fabryki prawdopodobnie warto postawić na odpowiednie oprogramowanie przemysłowe i narzędzia, np. czujniki do zbierania danych, które będą odpowiadać obecnym potrzebom użytkownika końcowego, np. zbierania rzetelnych danych z linii produkcyjnej. Warto wybrać rozwiązanie, które posiada możliwość dalszego rozwoju w zależności od wyzwań, jakie będzie stawiać przyszłość, np. rozszerzenie systemu klasy SCADA o algorytmy sztucznej inteligencji do optymalizacji zużycia energii. Na rynku polskim i zagranicznym pojawia się wiele narzędzi wspomagających cyfryzację. Przykładową firmą współpracującą z ASTOR, jest AVEVA (wcześniejszy Wonderware), której portfolio zawiera narzędzia do cyfryzacji zakładów na różnych poziomach: od maszyny czy pojedynczego urządzenia pomiarowego, aż do całych fabryk umiejscowionych w różnych lokalizacjach. Umożliwiają wdrożenie podstawowych funkcjonalności, takich jak zbieranie i wizualizacja danych, aż po rozwiązania oparte na chmurze i sztucznej inteligencji, zapewniając integrację z zewnętrznymi systemami. Warto jednak pamiętać, iż inicjatywy wytypowane podczas badania ADMA nie narzucają konkretnego dostawcy, a jego wybór jest w pełni zależny od firmy przechodzącej proces cyfrowej transformacji.
Autor:
Małgorzata Rzadzik, Młodszy specjalista ds. wsparcia i rozwoju sprzedaży systemu w ASTOR
Absolwentka wydziału mechanicznego oraz wydziału zarządzania na Akademii Górniczo-Hutniczej w Krakowie. W ASTOR od 2 lat. Jednym z jej kluczowych obszarów działania w zakresie Przemysłu 4.0 było wspieranie w przeprowadzaniu badania dojrzałości cyfrowej dzięki metodologii ADMA. w tej chwili na stanowisku młodszego specjalisty ds. wsparcia i rozwoju sprzedaży systemu przemysłowego w ASTOR.