Produkcja wsadowa jest metodą produkcji, która prowadzi do wytworzenia określonej ilości produktu poprzez poddanie surowców wejściowych uporządkowanemu zestawowi operacji technologicznych. Proces wsadowy przebiega ściśle według specyfikacji i receptur. Na początku surowce są dozowane do naczynia przetwarzającego, którym może być mieszalnik lub reaktor, w którym poddawane są obróbce (np. mieszaniu, obróbce cieplnej lub chemicznej). zwykle mamy do czynienia z całą linią urządzeń przetwarzających. Gotowy produkt – zwykle w sposób automatyczny – trafia do zbiorników lub cystern załadowczych.
Na każdym z etapów procesu realizowana jest kontrola jakości. W chwili, gdy wytworzenie całej partii jest zakończone, można rozpocząć przetwarzanie nowego wsadu surowców.
Wsadowe metody produkcji wykorzystuje się m.in. w produkcji materiałów budowlanych, w przemyśle chemicznym, farmaceutycznym i spożywczym.
Produkcja wsadowa a proces ciągły
Produkcja ciągła różni się od wsadowej tym, iż – jak sama nazwa wskazuje – produkty wytwarzane są w sposób ciągły. Surowce w tym przypadku są nieustannie dozowane do instalacji, a następnie przetwarzane, a gotowy produkt – również w sposób ciągły – jest transportowany do zbiorników magazynowych.
Produkcja ciągła charakteryzuje się zwykle większym wolumenem – produkujemy pojedynczy produkt w dużych ilościach. W przypadku produkcji wsadowej produkowane ilości są mniejsze, ale za to łatwiej zmienić asortyment, tzn. rodzaj produkowanego produktu. Przykładem produkcji ciągłej będzie np. linia wytwarzania amoniaku lub oleju napędowego. Z kolei przykładem produkcji wsadowej będzie linia produkcji farb, która może wykonywać różne rodzaje farb na zamówienie klienta.
Wady i zalety obu rodzaju procesów produkcyjnych
Oba te rodzaje procesów produkcyjnych mają swoje plusy i minusy. Produkcję ciągłą łatwiej jest zautomatyzować, ponieważ jest ona zaprojektowana do wyrobu konkretnego produktu. W efekcie potrzebna jest mniejsza liczba operatorów do obsługi takiej instalacji. Pracuje ona z reguły bez przerw, a więc 24 godziny na dobę, 7 dni w tygodniu – przestoje są bardzo rzadkie. Oznacza to, iż koszt produkcji na jednostkę produktu jest niski.
Wadą procesu ciągłego jest z pewnością wysoki koszt budowy samej instalacji. Należy też zauważyć, iż minusem może być również cecha, którą powyżej wymieniliśmy jako zaletę – a więc fakt, iż instalacja przeznaczona jest wyłącznie do produkowania jednego produktu. Jego zmiana na inny wymaga przebudowania instalacji albo wręcz jest niemożliwa.
Tej wady nie ma produkcja wsadowa, gdzie jedna instalacja może być wykorzystywana do wytwarzania większej liczby produktów, choćby kilkuset. Możemy produkować np. farby w kilkudziesięciu różnych kolorach. Linia tego typu jest więc bardzo elastyczna – można ją gwałtownie przekonfigurować do produkcji dowolnego produktu, na który jest aktualnie zapotrzebowanie. Ułatwia to również kontrolę jakości, którą możemy prowadzić na każdym etapie procesu, gwałtownie wprowadzając poprawki.
Przy wszystkich swoich zaletach produkcja wsadowa jest trudniejsza w automatyzacji, wymagając również z reguły większego personelu operatorskiego. Z oczywistych względów większa jest też liczba przestojów takiej linii – konieczne są przezbrojenia i inne czynności przygotowawcze przy każdej zmianie produkowanego asortymentu. Trzeba też pamiętać, iż w produkcji wsadowej łatwiej jest o pomyłki, które nam zwykle nie grożą w produkcji ciągłej, gdy bez przerwy produkujemy ten sam produkt. A każdy błąd jest bardzo kosztowny. o ile zepsujemy cały wsad, nadaje się on wyłącznie do utylizacji, za którą trzeba dodatkowo zapłacić.
Systemy informatyczne wspomagające produkcję wsadową
Wymienione wyżej wady produkcji wsadowej charakterystyczne są jednak przede wszystkim dla zakładów o niskim poziomie automatyzacji. Nowoczesne systemy automatyki i informatyki przemysłowej pozwalają skutecznie zminimalizować ich znaczenie. Skorzystać na tym mogą producenci wysoko wyspecjalizowanych produktów, takich jak żywice, poliole, suplementy diety czy kolorowe farby. Na tego typu rynkach trendy bardzo gwałtownie się zmieniają, a w takim przypadku zalety produkcji wsadowej mogą okazać się bardzo cenne. Skuteczny system sterowania i zarządzania pozwala na szybkie rekonfiguracje linii produkcyjnej, a tym samym na szybką odpowiedź na zmieniające się zapotrzebowanie.
Korzyści z automatyzacji i informatyzacji procesu wsadowego
Pierwszą istotną korzyścią jest zapewnienie stałej i zgodnej ze specyfikacją jakości produktów, niezależnie od partii produkcyjnej. System informatyczny steruje sekwencją wykonywania zadań, a większość operacji wykonywana jest automatycznie. o ile konieczna jest ingerencja operatora, otrzymuje on jasne informacje i polecenia, a system rejestruje efekty wykonanych przez niego czynności.
Druga korzyść to lepsze wykorzystanie zasobów i poprawa efektywności operacyjnej. System dynamicznie przypisuje lokalizację surowców do zbiorników, dzięki czemu produkcja jest realizowana zgodnie ze specyfikacją receptury niezależnie od położenia surowców. Również wykorzystanie urządzeń jest bardziej efektywne – każde urządzenie, które zakończyło działanie w ramach jednej partii produkcyjnej, jest od razu dostępne dla kolejnego wsadu.
Niezwykle istotne jest zapewnienie większego poziomu bezpieczeństwa produkcji. Jedną z funkcji sytemu jest zarządzanie blokadami (process and safety interlocks), gwarantujące bezpieczeństwo całej instalacji oraz personelu. Dzięki zastosowaniu redundancji na każdym z poziomów, a więc na poziomie automatyki, wizualizacji oraz systemu recepturowania, a także dzięki zastosowaniu wirtualizacji, system zapewnia ciągłość prowadzenia procesu.
Genealogia produkcji
Wszystkie informacje związane z przebiegiem procesu produkcyjnego są rejestrowane w bazie danych. Dotyczy to również danych dotyczących wykonywania poszczególnych partii produktów. Rejestr zawiera genealogię produktów, zadania wykonane podczas produkcji, parametry faz, zmiany statusów sprzętu (rezerwacje urządzeń i udostępnienia do produkcji), czynności i komentarze operatorów, a także kompletny zapis wszystkich wydarzeń. Automatyczny sposób zapisywania i udostępniania danych eliminuje papierowy przepływ dokumentów.
Zautomatyzowany proces budowania aplikacji
Dobrze zaprojektowany system zarządzania produkcją wsadową jest otwarty, łatwy do modyfikowania i rozbudowy oraz prosty w obsłudze przez operatorów. Przykładowo autorskie narzędzia Control-Service pozwalają znacznie zredukować czas tworzenia i uruchamiania aplikacji oraz zminimalizować prawdopodobieństwo popełnienia błędów. Graficzny interfejs receptur umożliwia łatwe i szybkie tworzenie, kopiowanie i modyfikowanie receptur – co ważne, bez konieczności angażowania programistów. Znacząco skraca to czas i obniża koszty uruchamiania produkcji nowych wyrobów.
Szczególną zaletą systemu jest intuicyjny interfejs użytkownika, który pozwala w bezpieczny i uporządkowany sposób kontrolować procesy zachodzące w instalacji. Wszystkie zdarzenia zachodzące w instalacji, takie jak alarmy, blokady technologiczne czy kroki sekwencji, są w intuicyjny i czytelny sposób pokazywane operatorowi, co ułatwia dokładne śledzenie procesu produkcyjnego.
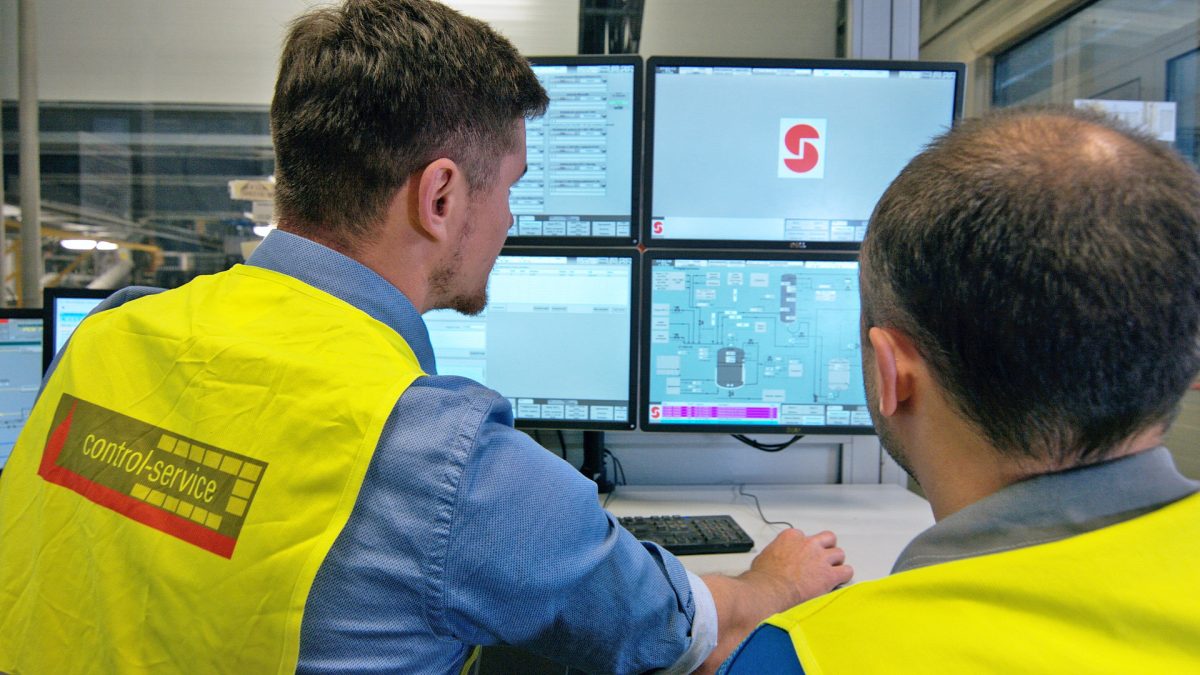
Symulator procesu wsadowego
Elementem systemu zarządzającego produkcją wsadową może być symulator procesu produkcyjnego. Jest to kompletny, wirtualny model fabryki, który dokładnie odwzorowuje cały proces wytwarzania. Taki symulator (zwany też „cyfrowym bliźniakiem” – digital twin) umożliwia gruntowne przetestowanie całego systemu przed jego implementacją na obiekcie. Możemy zweryfikować poprawność działania wszystkich elementów i skontrolować zależności pomiędzy nimi. Możemy sprawdzić funkcjonowanie blokad i prawidłowość przebiegu procesów krok po kroku, w zależności od wyboru różnych produktów i receptur.
Wszystko to jest możliwe całkowicie wirtualnie, co oznacza, iż możemy przeprowadzać testy bez ryzykowania strat wynikających z uszkodzenia instalacji czy złej jakości gotowego produktu. Dzięki symulatorowi można znacząco skrócić czas uruchomienia instalacji, tak by np. wdrożenie trwało 2 dni zamiast 2-3 tygodni.
Kolejną zaletą cyfrowego symulatora procesu jest możliwość szkolenia personelu z zakresu obsługi całego systemu. Dzięki temu pracownicy mogą nauczyć się wszystkiego, co niezbędne, w komfortowych warunkach i bez ryzyka popełnienia kosztownych błędów. Po zakończeniu takiego wirtualnego szkolenia i nabraniu odpowiedniego doświadczenia operatorzy mogą zacząć bezpiecznie sterować rzeczywistą produkcją.
Cyfrowy symulator produkcji pozwala wreszcie na łatwe testowanie wszelkich planowanych modyfikacji w procesie. Możemy łatwo sprawdzić, jaki będą one miały wpływ na produkcję, czy są bezpieczne i czy przyniosą oczekiwane efekty. Dopiero po symulacyjnym zweryfikowaniu wprowadzamy zmiany w rzeczywistej instalacji. Pozwala to obniżyć koszty i zminimalizować ryzyko.
Podsumowanie
Systemy produkcji wsadowej umożliwiają szybką reakcję na zmiany zapotrzebowania ze strony klientów. Ułatwiają tworzenie nowych produktów oraz modyfikowanie już istniejących – poprzez łatwe wprowadzanie korekt w recepturach ich wytwarzania. Systemy takie świetnie sprawdzają się tam, gdzie mamy do czynienia z mieszaniem i obróbką termiczną, ciśnieniową oraz chemiczną wielu składników w celu uzyskania gotowego produktu, a więc w przemyśle chemicznym, farmaceutycznym, spożywczym i nie tylko.
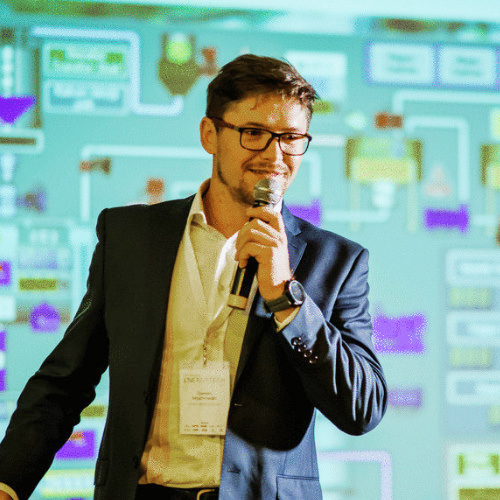
Autor:
Damian Majchrowski, Control Service
Kierownik ds. rozwoju w zakresie systemów produkcji wsadowej w Control Service.