Rosnące znaczenie TPM w polskich firmach
W polskim środowisku przemysłowym, strategia Total Productive Maintenance (TPM) nabiera coraz większego znaczenia. Liczba firm w Polsce wdrażających TPM systematycznie rośnie. Według raportu Polskiego Instytutu Lean Manufacturing, w 2023 roku 70% firm produkcyjnych deklarowało, iż wdrożenie TPM będzie kluczowym elementem ich strategii utrzymania ruchu. Wskazuje to na wyraźne zainteresowanie tą koncepcją i jej rosnące znaczenie dla polskich przedsiębiorstw. Firmy w Polsce wdrażają TPM w różnych celach. Przede wszystkim dążą do poprawy wydajności produkcji, zmniejszenia strat i kosztów oraz zwiększenia konkurencyjności na rynku. Często istotny jest również aspekt edukacyjny, związany z większym zaangażowaniem pracowników, z różnych działów firmy, w zakresy odpowiedzialności utrzymania ruchu.
Przypomnienie o założeniach TPM
TPM, które jest jedną z odmian filozofii Lean Manufacturing, opiera się na założeniu ciągłej optymalizacji procesów. Skupia się przy tym na zwiększaniu zaangażowania pracowników w wybranych dziedzinach utrzymania ruchu. Głównym celem TPM jest osiągnięcie możliwie maksymalnej efektywności produkcji poprzez minimalizację strat, związanych z nieplanowanymi przestojami, zwiększenie poziomu jakości wyrobów gotowych oraz zapewnienie bezpieczeństwa pracy poprzez zaangażowanie pracowników.
Należy pamiętać, iż TPM obejmuje również założenia związane z:
- Nadawaniem autonomii pracownikom w zakresie utrzymania ruchu. Umożliwia podejmowanie decyzji i działań pozwalających na wykonywanie niektórych czynności konserwacyjnych przez operatorów.
- Tworzeniem harmonogramów działań konserwacyjnych i wymian komponentów terminowych. Dostarcza również wszystkie informacje najważniejsze do realizacji działań.
- Optymalizacją działań prewencyjnych. Obejmuje harmonogramowanie prac pozwalające minimalizować ryzyko awarii na bazie danych historycznych oraz aktualnych stanów maszyn.
- Zapewnieniem i utrzymaniem jakości. Pozwala na stałą kontrolę i monitorowanie procesów oraz umożliwia dbanie o odpowiednie parametry jakościowe na każdym etapie produkcji.
- Skuteczną komunikacją między działami. Zapewnia płynny przepływ informacji i współpracę między pracownikami z różnych obszarów.
- Stałą weryfikacją i ciągłą edukacją pracowników, również z podstawowych zakresów pracy innych działów.
- Pilnowaniem aktualności procedur oraz budowaniem wśród pracowników świadomości znaczenia ich działań dla całej organizacji.
TPM to nie jedna magiczna technika…
To zmiana mentalności i świadomość wspólnej organizacji!
Jeżeli chcesz dowiedzieć się więcej o podstawowych założeniach sprawdź nasz wcześniejszy artykuł Poznaj Total Productive Maintenance (TPM), czyli sposób na bezpieczne i efektywne Utrzymanie Ruchu | Biznes i Produkcja (astor.com.pl)
TPM a mentalność pracowników
TPM to nie tylko narzędzie. To przede wszystkim sposób myślenia i postępowania. Dlatego wdrożenie TPM wymaga zmiany mentalności, zarówno pracowników jak i kierownictwa. Kluczowym elementem jest zaangażowanie wszystkich, na każdym szczeblu organizacji. Wiąże się to z budowaniem świadomości – dział produkcji jest odpowiedzialny nie tylko za wielkość produkcji, ale również za swoje miejsce pracy.
Przykład: Nadanie operatorom i brygadzistom odpowiedzialności za czystość maszyn, ich niezawodność oraz pilnowanie czy przechodzą niezbędne do prawidłowego funkcjonowania regularne przeglądy.
Wprowadzenie TPM wymaga otwartej komunikacji między działami. Ważnym elementem jest też edukowanie, z czego rozliczani są pracownicy innych działów i co jest dla nich ważne przy realizacji celów. Buduje to poczucie, iż cała organizacja funkcjonuje jak jeden organizm.
Przykład: Spotkania działu produkcji i działu utrzymania ruchu (DUR) obejmujące regularne szkolenia z zakresu utrzymania ruchu dla produkcji, spotkania o aktualizacjach dokumentacji i procedur, spotkania mające na celu wymianę pomysłów na ulepszenia pracy operatorów oraz analizy możliwości wykonania usprawnień przez DUR.
Elementem TPM jest również wzbudzanie u pracowników przekonania, iż ich głos jest istotny dla organizacji. Obejmuje to również komunikację z kierownictwem.
Przykład: Pracownicy działu utrzymania ruchu mają przypisane maszyny, za które są odpowiedzialni. Zgłaszają swoje uwagi oraz propozycje do kierowników swojego działu. Ci natomiast przedstawiają uwagi na spotkaniach z pozostałymi kierownikami.
Dlaczego CMMS jest idealnym narzędziem by rozpocząć wdrażanie TPM
Wdrożenie strategii TPM w firmie często zaczyna się od wyboru odpowiedniego narzędzia do zarządzania utrzymaniem ruchu. W tym kontekście System Zarządzania Utrzymaniem Ruchu (CMMS) jest idealnym rozwiązaniem. Dlaczego?
- Spełnia założenia pilnowania oraz standaryzacji procesów związanych z utrzymaniem ruchu. Należy do nich planowanie prewencyjne, jak i konserwacja oparta na stanie (Condition Based Maintenance).
- Pozwala na gromadzenie wszystkich informacji technicznych o maszynach, w tym historii i dokumentacji. Obejmuje to również informacje o częściach zamiennych, a choćby potencjalnej rentowności.
- Automatyzuje proces weryfikacji aktualności dokumentów oraz kwalifikacji pracowników. Rozsyła również powiadomienia do upoważnionych osób.
- Powiadamia odpowiednie działy w firmie. Na przykład, informuje dział utrzymania ruchu, o dodanych awariach i usterkach, dział produkcji o podjętych i zakończonych pracach, dział jakości o miejscach w procesie, gdzie mogą występować potencjalne błędy, a dział BHP o zdarzeniach potencjalnie niebezpiecznych.
- Spektrum raportowe systemów CMMS nie służy tylko do badań efektywności. Pozwala również na weryfikację prac, śledzenie historii zdarzeń, co w rezultacie prowadzi do optymalizacji procesów.
Co istotne, systemy CMMS posiadają specjalne platformy dla konkretnych użytkowników. Dzięki temu każda osoba ma łatwy dostęp do funkcji dotyczącej jej pracy, ale też możliwość wglądu do pozostałych danych w celach edukacyjnych.
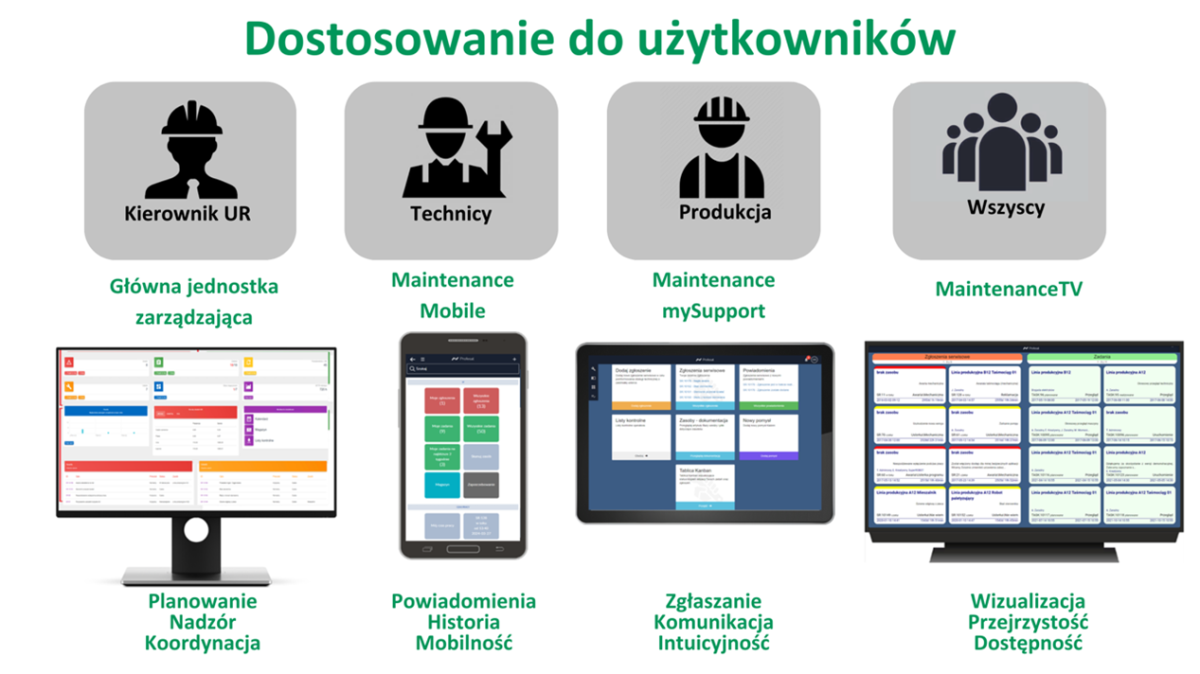
Dalsze możliwości użycia CMMS do przyśpieszania wdrożenia TPM
Filarem wdrożenia TPM jest wdrażania metody 5S. Dlatego system CMMS może wspierać nie tylko DUR, ale również operatorów maszyn we wprowadzaniu nowych zasad pracy. System CMMS może oferować takie funkcje jak:
- Lista czynności do wykonania przed pracą
- Podgląd narzędziowni produkcji
- Cyfrowe tablice informacyjne, numery alarmowe czy tablice Kaban
W niektórych przypadkach operatorzy mogą własnoręcznie dokonywać drobnych napraw. Prowadzi to do odciążenia działu UR, co z kolei zwiększa opłacalność pracy całej organizacji.
Innym aspektem jest automatyzacja procesów planowania i harmonogramowania działań konserwacyjnych. Systemy mogą generować zlecania przeglądów/inspekcji na podstawie liczników, spisywanych z maszyn czy obchodów technicznych. Następnie przypomnienia w formie powiadomień systemowych, mailowych czy SMS-owych, trafiają do wykonawców na podstawie ich dostępności w pracy. CMMS informuje również o zaległościach w pracach oraz proponuje alternatywnych wykonawców.
Specjalne raporty dostępne w systemie CMMS pozwalają na wizualizację kompetencji pracowników, w tym poziomu zaawansowania umiejętności ogólnych czy obsługi konkretnych maszyn. Wspierają wykrywanie braków kadrowych oraz proponują nowe koncepcje związane ze szkoleniami. Raporty wspomagają również wykrywanie przyczyn awarii oraz mapowanie zdarzeń zbieżnych. Zapewniają podgląd wykonanych czyszczeń maszyny, a choćby umożliwiają wskazanie najbardziej zaawansowanych operatorów, czyli osób mających potencjał na znaczące wsparcie dla działu technicznego.
Powiązanie nie tylko z filozofią TPM, ale i ze strategią cyfryzacji to zdecydowanie przyszłościowe aspekty systemu CMMS, który wspiera również możliwość integracji systemu z innymi rozwiązaniami w organizacji.
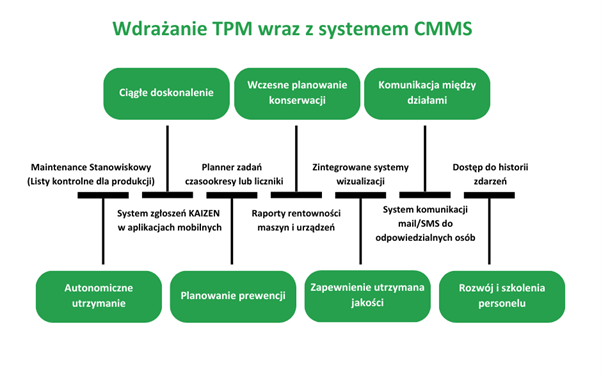
Przy integracji ze SCADĄ (system wizualizujący i nadzorujący przebieg procesu technologicznego lub produkcyjnego) pozwala na automatyczne generowanie zleceń przeglądu na podstawie godzin pracy, przebiegu, a choćby dodatkowych parametrów.
Przy integracji z czujnikami podłączonymi do maszyny (w tym sensorami drgań, temperatury, akustyki) mogą generować automatycznie do systemu zlecania dotyczące usunięcia usterek lub zdarzeń przed-awaryjnych. Przyspiesza to przekazanie informacji oraz pozwala na wizualizację, np. na ekranach w warsztatach utrzymania ruchu.
Pry integracji z systemami ERP (Enterprise Resource Planning) pozwala na automatyczne przesyłanie informacji związanych z planowaniem zasobów przedsiębiorstwa. Obejmuje to przesyłanie danych magazynowych do innych działów, w tym działu zamówień, przesyłanie informacji o zmianach w planie produkcyjnym, dokonanych przez planistów. Niezwykła jest też możliwość projektowania działań optymalizujących na podstawie sumarycznych danych związanych z kosztami, uzyskanych z systemu ERP oraz danych związanych z efektywnością maszyn i pracy, dostępnych w systemie CMMS.
Elastyczność! Jednym z elementów, który najbardziej przyczyni się do przyśpieszenia wdrożenia TPM w organizacji przez system CMMS, jest możliwość modyfikacji parametrów. Pozwala ona na dostosowanie systemu do unikalnych procesów wewnętrznych w organizacji. Pamiętajmy, iż pomimo pewnych podobieństw pomiędzy firmami tej samej branży, każda organizacja ma własną specyfikę. Warto pamiętać o pewnego rodzaju wyjątkowości organizacji, szczególnie gdy tworzymy nowe standardy pracy.
Wdrożenie Total Productive Maintenance (TPM) przy wsparciu Systemu Zarządzania Utrzymaniem Ruchu (CMMS) przynosi realne korzyści dla polskich firm. To nie tylko optymalizacja procesów, to również budowanie kultury ciągłego doskonalenia. Dlatego ważne jest, by zawsze mieć wizję rozwoju. Zainwestujmy w narzędzia, takie jak CMMS, które wspierają nasze cele i umożliwiają osiągnięcie sukcesu. Gotowi na transformację?