Kopalnia Soli Kłodawa S.A. działa od 1949 roku. To największy krajowy producent soli kamiennej w Polsce, z siedzibą w Kłodawie. Wydobycie rozpoczęto w 1956 roku a w 2019 r. firma świętowała jubileusz 70-lecia działalności. Kopalnia jest także atrakcją turystyczną, ponieważ od 2004 roku udostępnia zwiedzającym najgłębiej położoną – 600 m pod ziemią – atrakcyjną trasę turystyczną, a także organizuje podziemne koncerty muzyczne i inne wydarzenia dla lokalnej społeczności.
Kopalnia prowadzi eksploatację złóż tradycyjną metodą górniczą, która pozwala w pełni zachować naturalne walory soli. Aktualne wydobycie to ok. 650 tysięcy ton rocznie. Wydobyty surowiec trafia na powierzchnię, gdzie odbywa się pakowanie a następnie trafia do magazynów składowania i magazynów handlowych o łącznej pojemności 100 tys. ton.
Kruszenie, mielenie, sortowanie odbywa się bez stosowania zabiegów chemicznych. Proces paletyzacji opakowań soli dla odbiorców i sieci handlowych odbywa się metodą manualną i zrobotyzowaną.
W zakładzie przeróbki mechanicznej soli od kilku lat funkcjonuje 5 stanowisk zrobotyzowanej paletyzacji worków 25- i 50-kilogramowych oraz 10-kilogramowych lizawek dla zwierząt.
Nowy rozdział technologicznego rozwoju
W ostatnim czasie kierownictwo kopalni postanowiło uzupełnić istniejące rozwiązania stawiając na wdrożenie nowego, zrobotyzowanego stanowiska do paletyzacji wraz z systemem transportu wewnątrzzakładowego. System został rozbudowany wokół robota Kawasaki Robotics RD080N. Projekt koordynowany przez ASTOR we współpracy z Partnerami trwał od czerwca 2021 do grudnia 2021. Najnowszy system automatyzuje następujące elementy procesu produkcyjnego:
- paletyzację
- transport palet przy pomocy podajników rolkowych
- zabezpieczanie folią palety z produktem końcowym
- automatyczne naklejanie etykiety logistycznej
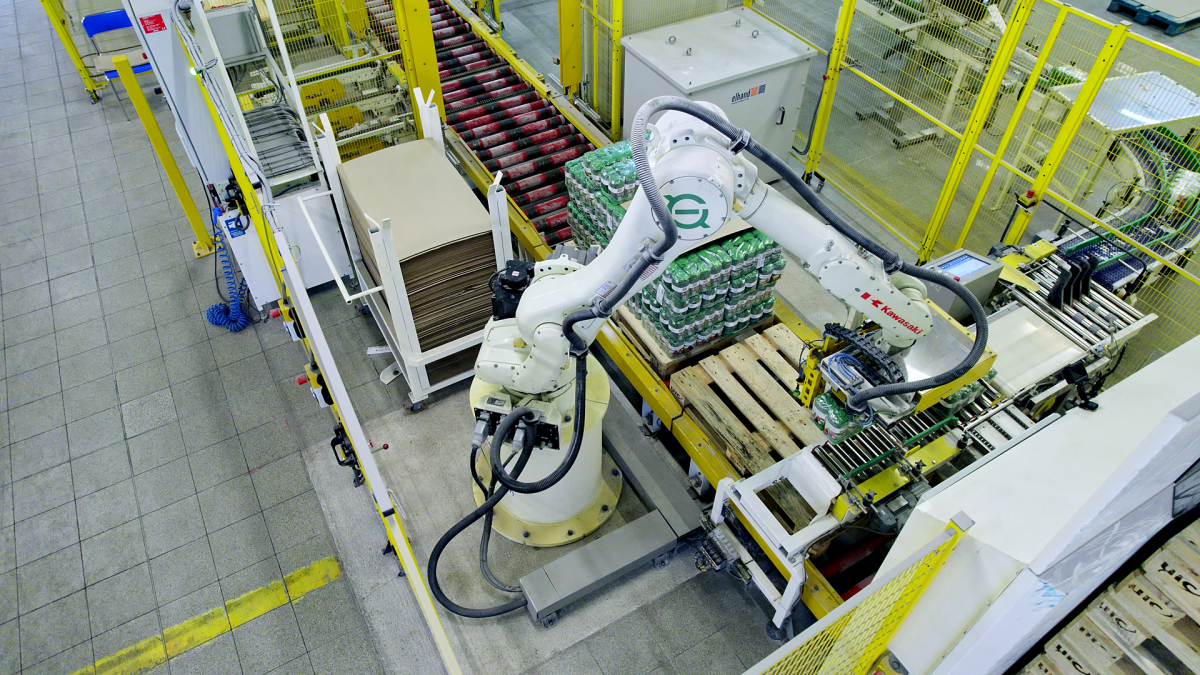
System obsługuje zgrzewki z woreczkami soli spożywczej o wadze 1 kg lub 1,1 kg. (zgrzewka zawiera 10 woreczków i waży 10 lub 11 kg), a jego wydajność to 7 ton spaletyzowanych produktów na godzinę.
Przekłada się to na ograniczenie ilości pracy fizycznej pracowników i zlimitowanie negatywnych skutków wymuszonej pozycji ciała, jednocześnie gwarantując wydajność na oczekiwanym poziomie.
Główne składowe systemu intralogistycznego to:
- robot paletyzujący Kawasaki Robotics RD080N wyposażony w chwytak ze stali nierdzewnej
- waga kontrolująca masę zgrzewek
- magazynek palet
- transportery paletowe
- owijarka palet
- etykieciarka palet
- kompletny system sterowania i panel operatorski do obsługi aplikacji
Na każdej z europalet robot układa 96 zgrzewek. Następnie, pełne palety są zabezpieczane przy użyciu foliowego kaptura oraz folii stretch przy użyciu owijarki talerzowej. Kolejnym elementem systemu jest automatyczna etykieciarka oraz przenośniki buforowe, na których palety oczekują na operatora wózka widłowego, który odwozi gotową, zabezpieczoną i oznaczoną paletę do magazynu.
Wizualizacja i realizacja projektu
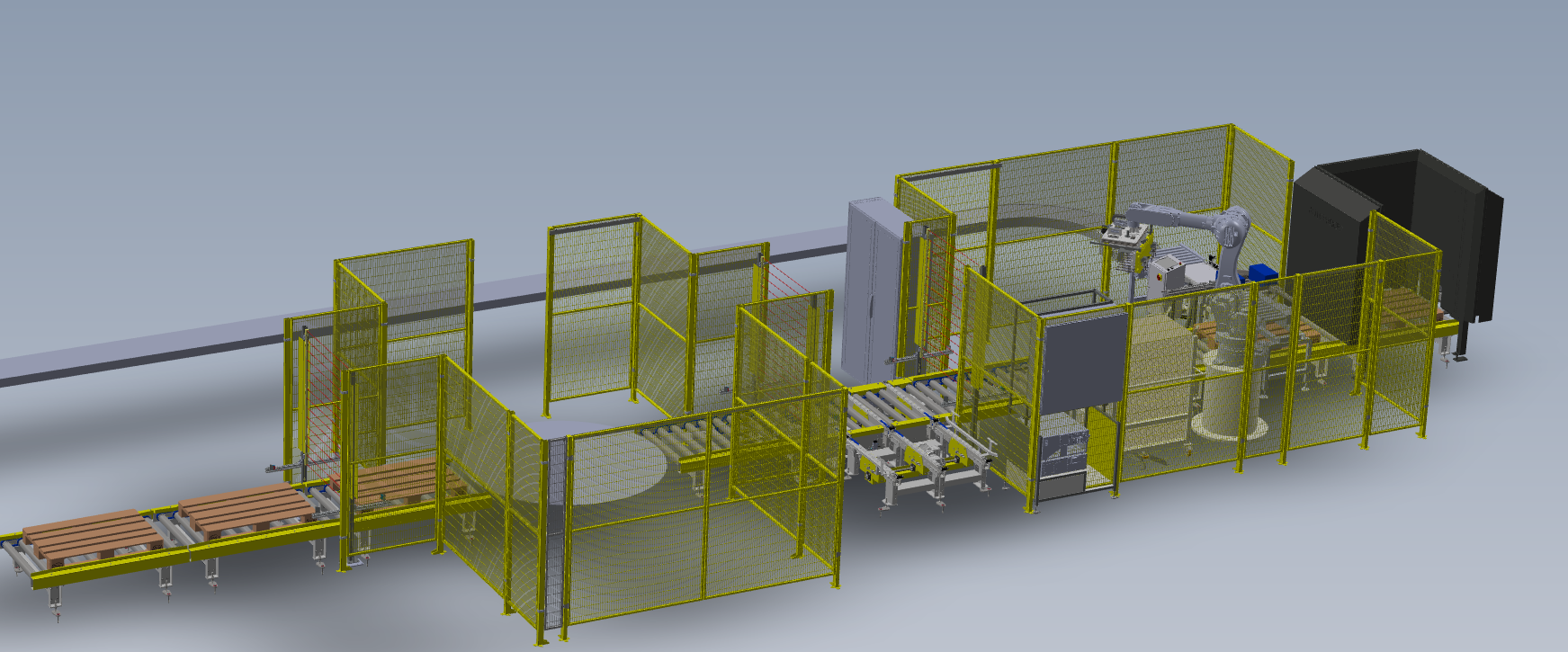
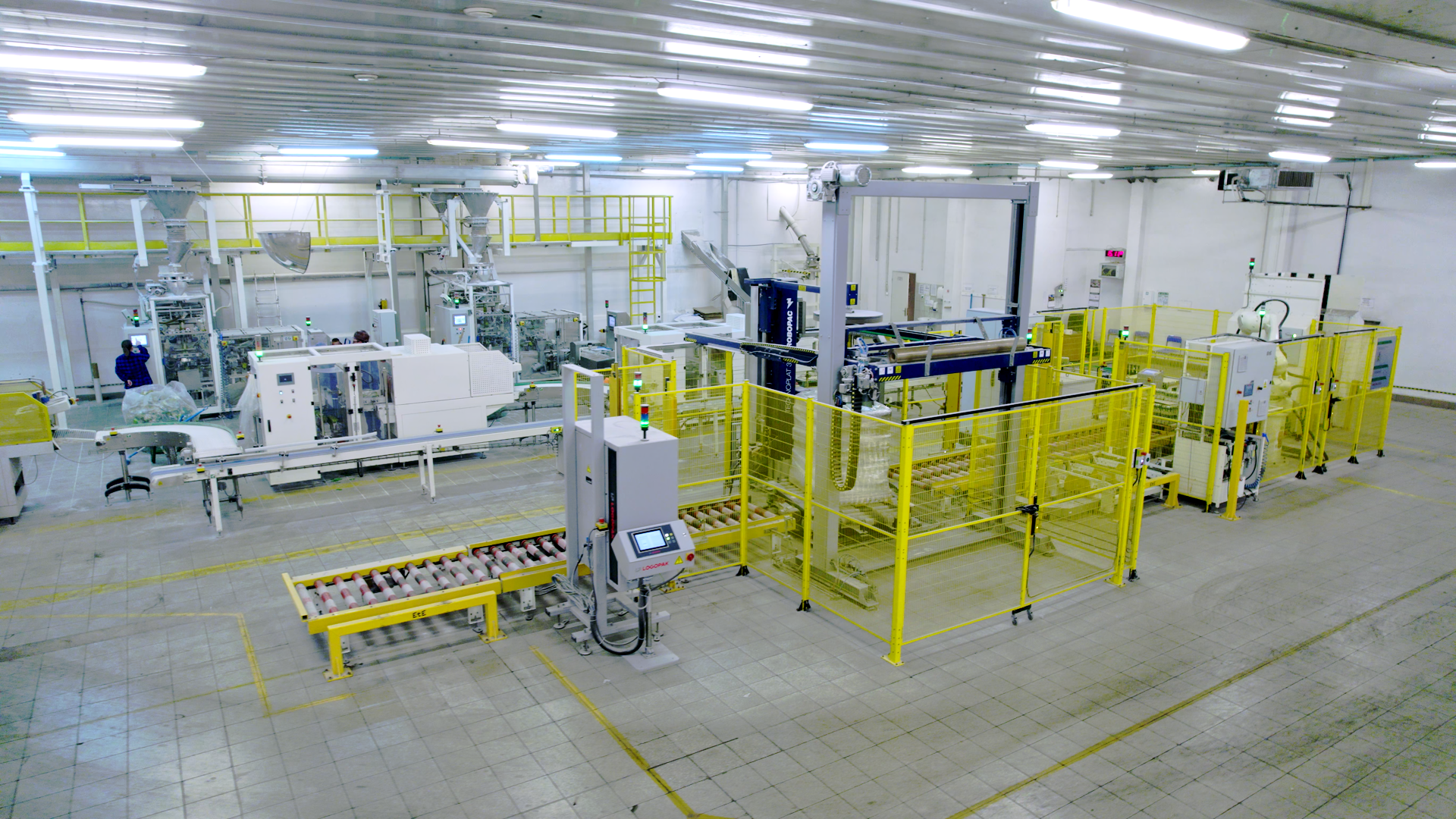

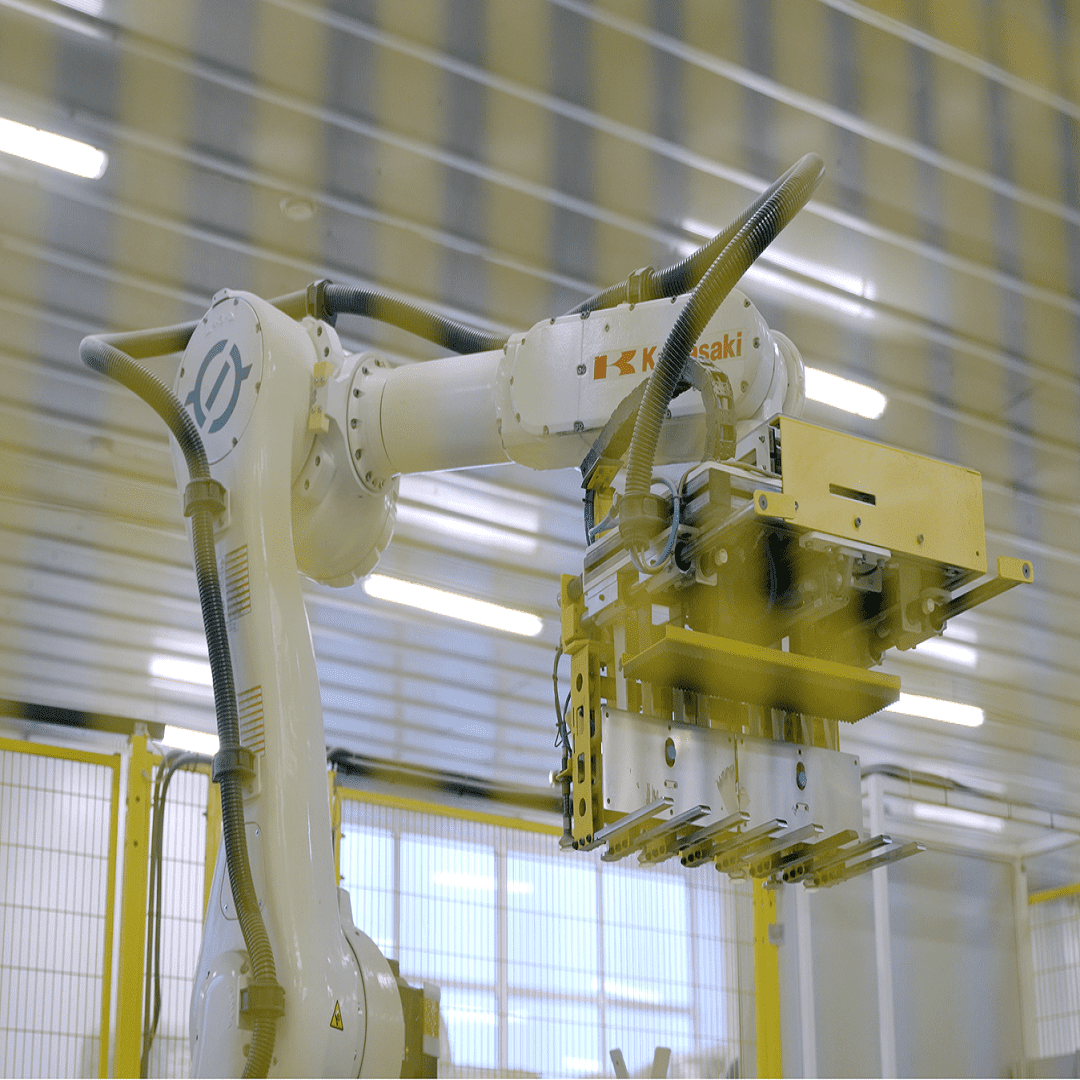
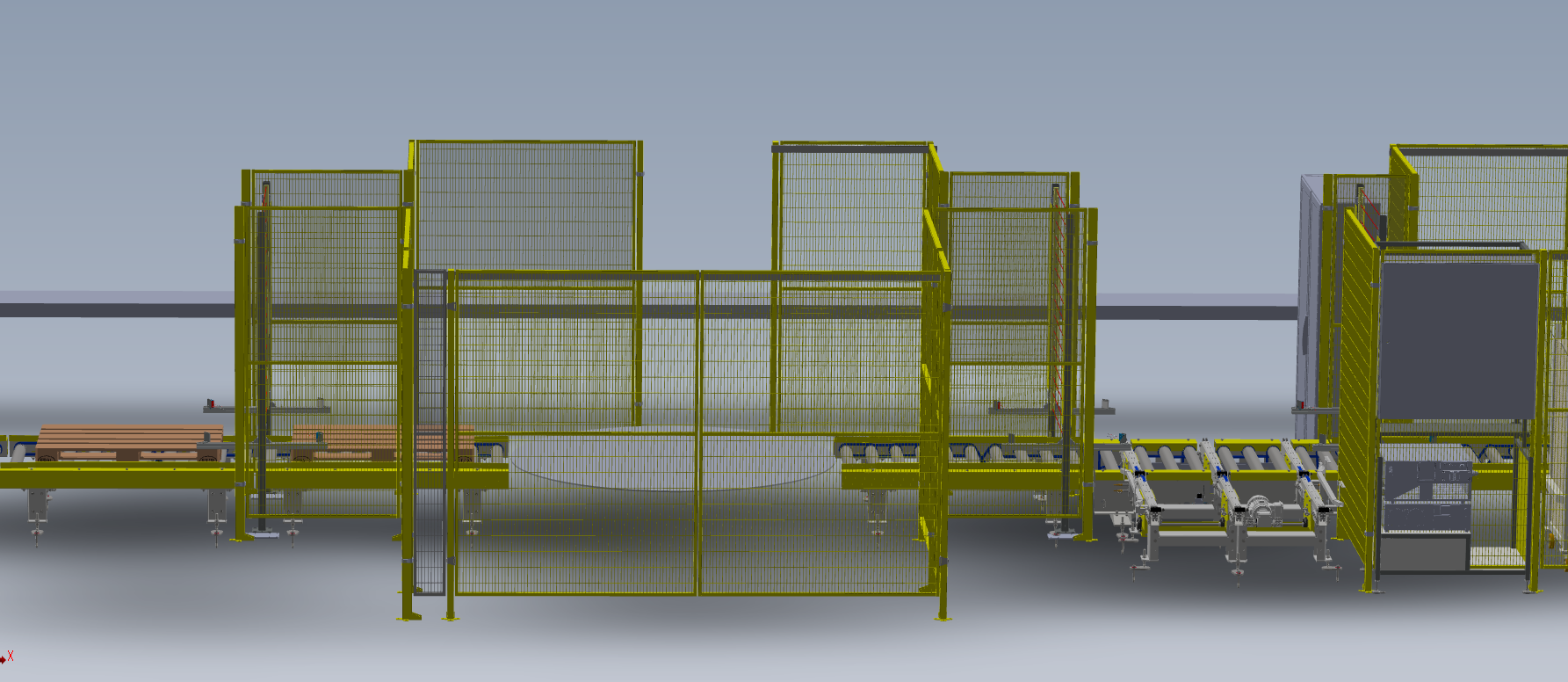
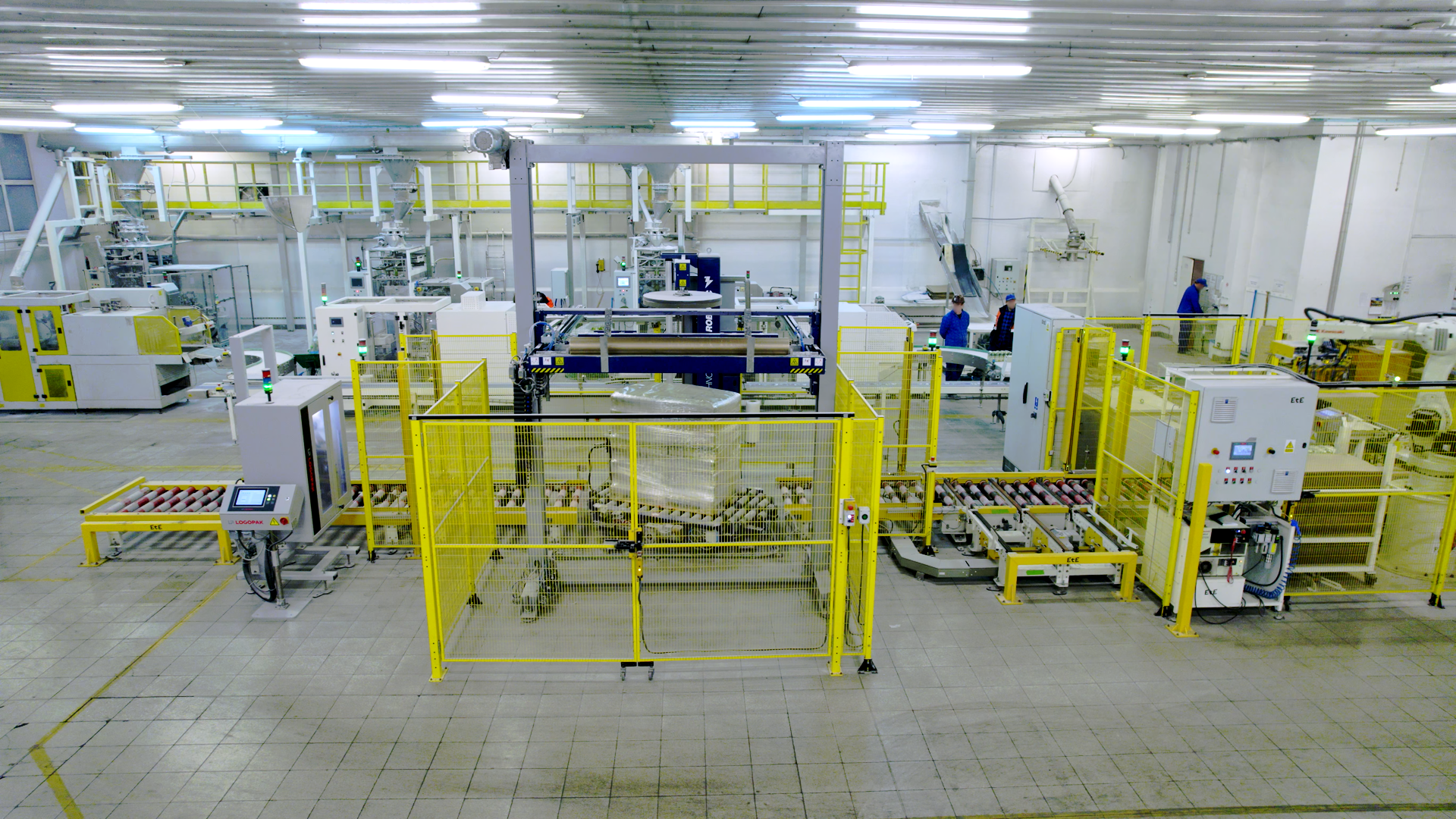
Wyzwania związane z realizacją projektu
Celem wdrożenia zrobotyzowanej paletyzacji była poprawa komfortu warunków pracy pracowników linii produkcyjnej przy jednoczesnym rozwiązaniu istniejących wyzwań. Trudne środowisko dla maszyn z powodu soli osiadającej niczym kurz wymagało umiejętnego doboru materiałów i maszyn, które gwarantują odpowiednią żywotność podzespołów.
W górnictwie standardowym zasilaniem jest 500V w związku z tym należało, także dostosować system do pracy w takim standardzie, a wszystkie te założenia udało się zrealizować w wyznaczonym czasie 6 miesięcy od podpisania umowy do odbiorów końcowych.
Zalety nowego rozwiązania
Efektywne działanie systemu jasno pokazuje korzyści. Dzięki zrobotyzowanemu stanowisku do paletyzacji poprawiły się warunki pracy pracowników produkcji, obecne zadania to kontrola działania systemu i zarządzanie aplikacją wdrożoną poprzez panel operatorski na linii produkcyjnej.
System obsługuje założoną wydajność produkcyjną, może pracować 24/7 dzięki czemu nie ma przestojów, a Klient może planowo realizować swoje zobowiązania.
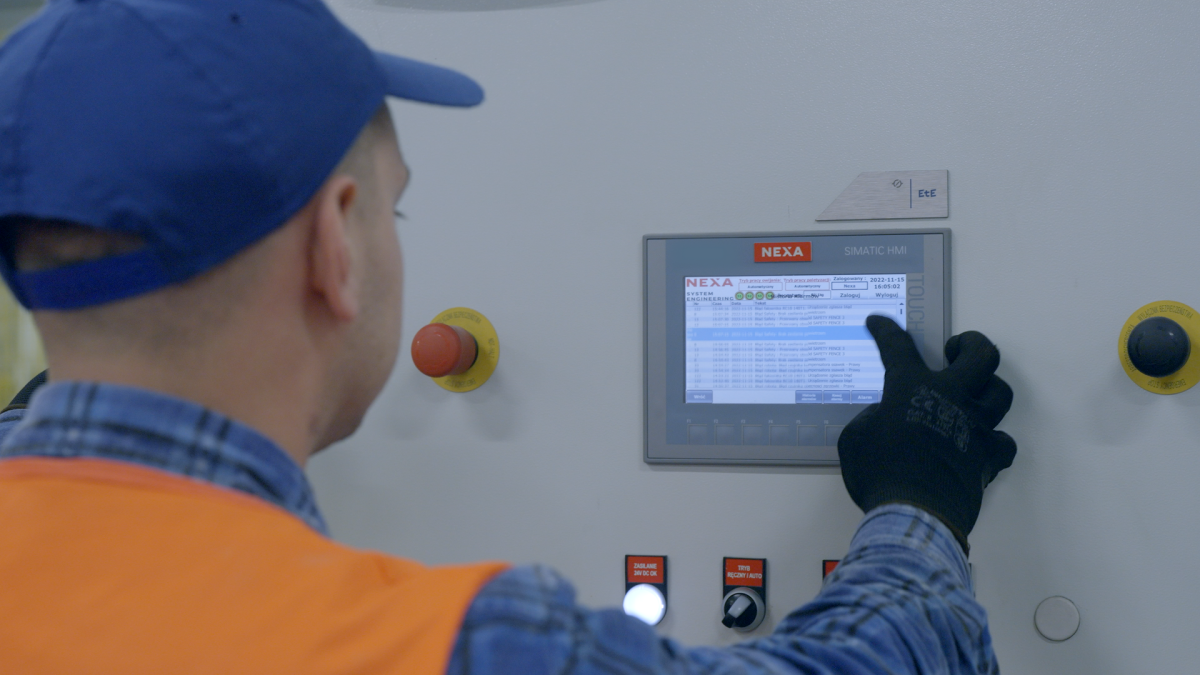
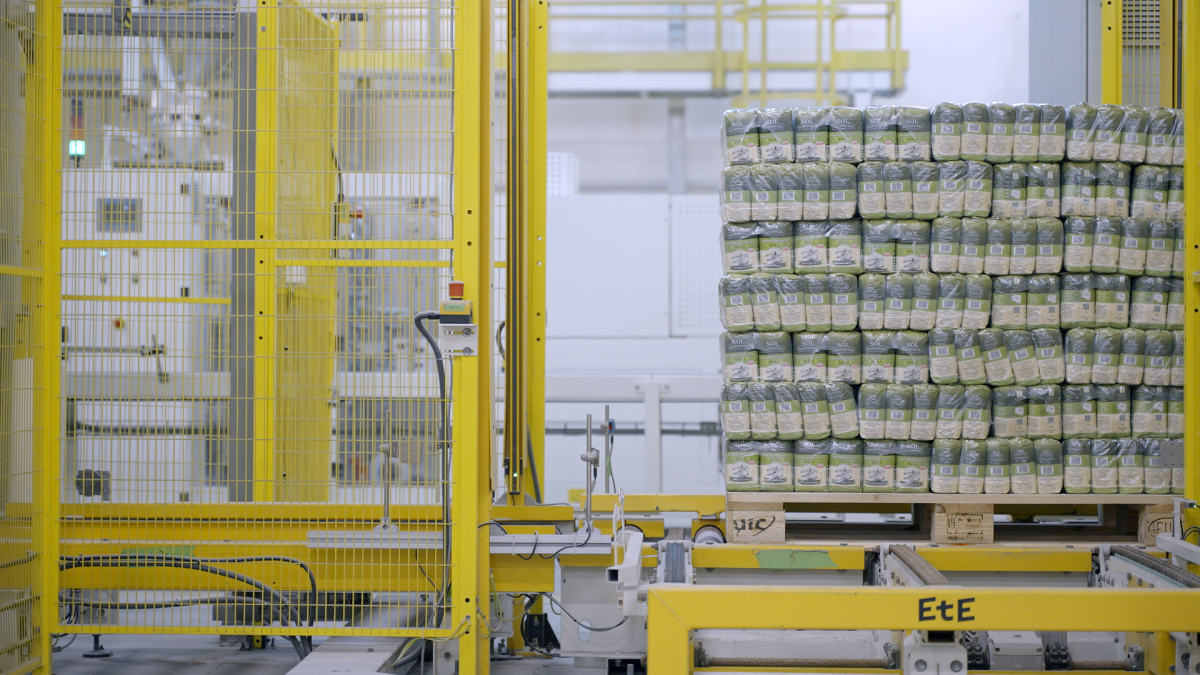
Zrobotyzowana paletyzacja – dlaczego jest tak ważna
Zrobotyzowane stanowiska paletyzacji wraz z systemem transportu wewnątrzzakładowego produktów gotowych, dobrze sprawdzają się w zakładach produkcyjnych. Paletyzacja zgrzewek, kartonów czy wiader projektowana jest pod indywidualne potrzeby zakładu.
Rozwiązania tego typu są trwałe, roboty przemysłowe mogą niezawodnie przez wiele lat, przenosić i układać produkty na paletach. Odciążają tym samym pracowników i gwarantują im większy komfort i bezpieczeństwo pracy.
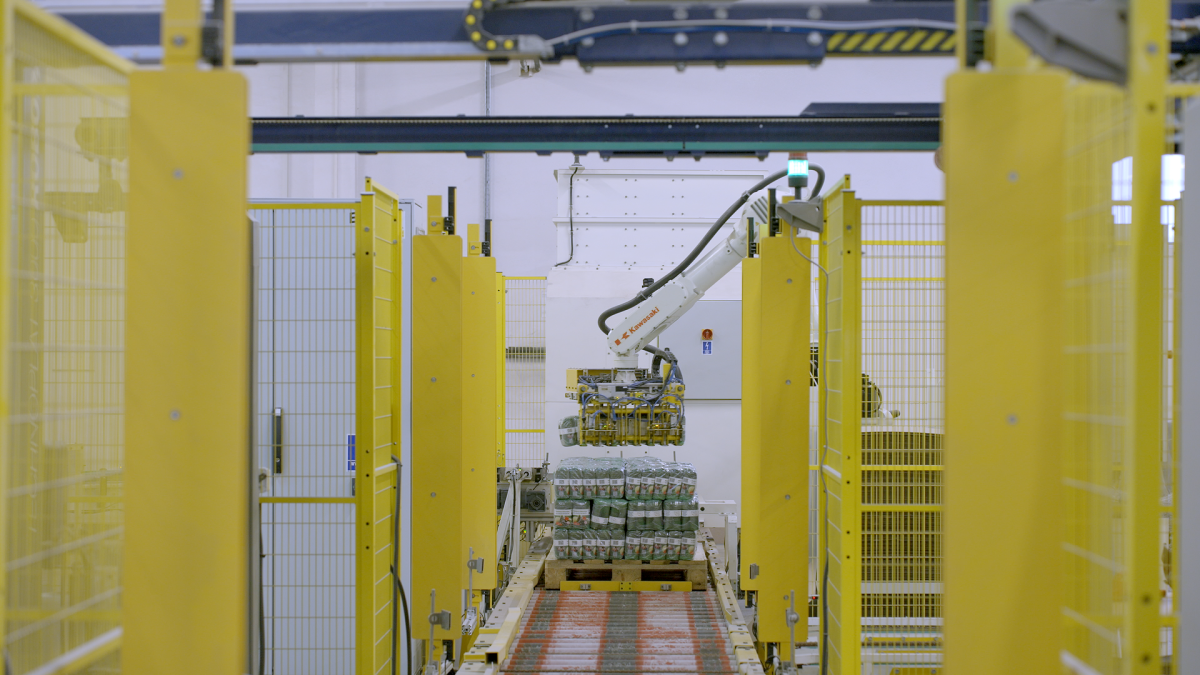
System transportu produktów gotowych do magazynu projektowany jest adekwatnie do oczekiwanych wydajności i wymagań danej branży.
„Przy projektowaniu systemów intralogistycznych zawsze dbamy o optymalizację wykorzystania przestrzeni produkcyjnej. Uwzględniamy specyfikę branży, indywidualne potrzeby klienta i wymaganą wydajność stanowiska. Dostarczona końcówka linii produkcyjnej zapewnia wysoką jakość i powtarzalność procesu w trudnych warunkach przemysłowych, przy wysokim wolumenie produkcji” – mówi Bartłomiej Kałuża, Kierownik ds. realizacji projektów inwestycyjnych, Dział Intralogistyki, ASTOR.
Przykład wdrożenia w Kopalni Soli Kłodawa pokazuje, iż zrobotyzowane stanowisko do paletyzacji jest cennym uzupełnieniem istniejących linii produkcyjnych, a także ważnym etapem w realizacji strategii rozwoju firmy.
Autor:
Kinga Tarsa, ASTOR, linia biznesowa Intralogistyka
Kontakt:
Damian Fryska, Dyrektor oddziału ASTOR Zachód
Z firmą ASTOR związany już blisko 10 lat. Odpowiedzialny za realizację projektów w zakresie automatyzacji i robotyzacji procesów produkcyjnych dla dużych przedsiębiorstw z ukierunkowaniem na intralogistykę i paletyzację oraz za współpracę z Partnerami wdrożeniowymi. Prowadził projekty związane z rozwojem bazy dydaktycznej dla edukacji, współpracuje z uczelniami wyższymi i centrami kompetencji, rozwijając ich możliwości kształcenia kolejnych pokoleń inżynierów. Od 2022 jest kierownikiem oddziału ASTOR Zachód, zarządzając pracą zespołu ekspertów w zakresie cyfryzacji i robotyzacji procesów produkcyjnych.