Jednym z ważniejszych wyzwań tego typu produkcji jest zapewnienie oczekiwanej wydajności linii montażowych. Jest to trudne zadanie, ponieważ komponenty pochodzą z wielu źródeł, a proces produkcji jest skomplikowany i wieloetapowy. W efekcie, przestoje, czy różnego rodzaju opóźnienia w jednym punkcie kumulują się w następnych, co znacząco zmniejsza efektywność całego zakładu. Dodatkowym utrudnieniem jest odpowiednie zgranie łańcuchów intralogistycznych, tak by surowce, podzespoły i gotowe produkty trafiały we adekwatne miejsce we adekwatnym czasie.
Wprowadzenie technologii cyfrowego bliźniaka pozwala zmierzyć się z tymi problemami. Wirtualna kopia linii produkcyjnej, montażowej, czy sieci intralogistycznej pozwala łatwo znaleźć przyczyny przestojów, modelować funkcjonowanie zakładu, przewidywać problemy w najbliższej przyszłości oraz gromadzić dane i na ich podstawie optymalizować pracę, a także planować modernizację, prowadząc testy nowych rozwiązań w przestrzeni wirtualnej.
Studia przypadku trzech polskich firm z branży przemysłowej
Cyfrowy bliźniak przewiduje przyszłość linii produkcyjnych
Firma X zajmuje się montażem zaawansowanych urządzeń z segmentu elektroniki użytkowej, zatrudnia około 1000 pracowników. Na omawianym obszarze ma 8 linii montażowych, po 10 stanowisk każda. Wyzwaniem było zapewnienie wysokiej efektywności wszystkich tych stanowisk. Cyfrowy bliźniak pozwolił się z nim zmierzyć.
Cyfrowa kopia wszystkich linii montażowych, działająca w firmie X zasilana jest danymi z MES (Manufacturing Execution System). Zarządzający linią może na ekranie komputera w czasie rzeczywistym obserwować, co się na niej dzieje, w jaki sposób realizowany jest przepływ podzespołów i produktów czy to, które stację są zablokowane. W omawianym przypadku system okazał się wyjątkowo użyteczny, ponieważ zarządzający m.in. rozbudowane statystyki dotyczące pracy każdej linii czy stanowiska oraz powody generowania przestojów.
Model linii montażowych odczytuje te stany ze wszystkich stanowisk i nie tylko pozwala na bieżąco rejestrować wskaźniki produktywności, ale też dokonuje predykcji na podstawie tych danych. Ustala, jak linia produkcyjna będzie zachowywać się w najbliższej przyszłości, w ciągu najbliższej godziny. To pozwala przewidywać problemy, które mogą się niedługo pojawić i na czas im zapobiegać.
Jeśli widoczne są przestoje, operator linii jest w stanie gwałtownie interweniować, wysłać pracownika, który odblokuje zator, ale też przygotować ludzi obsługujących pozostałe stanowiska na nadchodzące trudności. W przypadku omawianego zakładu produkcyjnego montowane urządzenia nie są seryjne, różnią się pewnymi parametrami, dlatego przewidywalność tego, co będzie działo się na linii montażowej w dłuższym horyzoncie jest ograniczona – wynika to bezpośrednio z sekwencji produktów pojawiających się na poszczególnych liniach. W innych zakładach przewidywania mogą dotyczyć dłuższego czasu – jest to zależne od horyzontu zdarzeń, jaki jesteśmy w stanie przewidzieć – zwłaszcza w kontekście realizacji założonego planu produkcyjnego.
Cyfrowy bliźniak wskazuje przyczyny przestojów
Firma Y zajmuje się montażem kompresorów do sprzętu AGD. Cyfrowy bliźniak pozwala zlokalizować stanowiska na linii montażowej, które generują przestoje w innych częściach zakładu, a tym samym optymalizować pracę całej linii. Klientowi zależało na podglądzie linii montażowej, żeby móc obserwować, co się na niej dzieje w czasie rzeczywistym. Kiedy jednak udało się uruchomić cyfrowego bliźniaka, który odwzorowywał pracę linii, pojawił się pewien niedosyt.
Sam podgląd był źródłem dość ograniczonych informacji. Przy współpracy z jednym z pracowników produkcji pojawił się pomysł, na rozbudowanie funkcji analitycznych cyfrowego bliźniaka.
Wiedziano wcześniej, iż na linii montażowej jest wąskie gardło – miejsce, w którym przepływ towarów był wolniejszy. Podjęto decyzję, by stworzyć system, który identyfikuje, stację będącą bezpośrednim „winowajcą” przestoju wąskiego gardła. Oczekiwano dostępu do informacji, jakie były powody zablokowania stacji i przestoju produkcji, lokalizacji wystąpienia problemu (przed wąskim gardłem czy bezpośrednio na nim). Zadaniem bliźniaka jest identyfikacja wszystkich stacji, które spowodowały zatrzymania wąskiego gardła na dłużej niż 7 sekund.
Dzięki temu powstał model, który na bazie informacji, iż konkretnych godzinach nastąpił 11-sekundowy postój wąskiego gardła, jest w stanie odwrócić ciąg przyczynowo-skutkowy i ustalić, które stanowisko jest odpowiedzialne za powstanie tego przestoju. Jest to możliwe dzięki wykorzystaniu danych pochodzących z systemu MES zawierających informację dotyczące stanów poszczególnych maszyn w czasie oraz trackingu przepływu poszczególnych produktów na linii. To może być np. maszyna, która była zepsuta i wymagała naprawy, ale zdarza, się, iż pracownik celowo lub przypadkiem zasłania fotokomórkę, co skutkuje błędnym wskazaniem „Zablokowany”. Model nie wyjaśnia, dlaczego to stanowisko miałoby być zablokowane, co demaskuje nieuczciwego lub nieuważnego pracownika.
Cyfrowy bliźniak wskazuje przyczyny przestojów
Firma Z jest integratorem robotów mobilnych AGV. Dzięki możliwości zaprojektowania systemu intralogistycznego dla klientów w przestrzeni wirtualnej, udało się znacząco skrócić czas rzeczywistego wdrożenia całej floty wózków AGV, dopasowanej do potrzeb konkretnego zakładu.
Cyfrowy model zakładu jest wykorzystywany jako swoisty poligon doświadczalny dla testowania działania systemu sterującego pojazdami autonomicznymi. Odwzorowując zakład produkcyjny, model pozwala przetestować, także w świecie wirtualnym, ile wózków AGV potrzeba, aby spełnić oczekiwania klienta, którymi trasami powinny być realizowane zadania transportowe, ile ładowarek będzie potrzebne, aby je obsłużyć.
Dzięki takiemu zastosowaniu bliźniaka możliwa jest znacznie szybsza implementacja rozwiązania u klienta. Firma wdraża już wirtualnie przetestowany układ transportowy, testowany na rzeczywistych produkcyjnych danych lub na założeniach podanych przez klienta („a co by było gdybyśmy produkowali 10% więcej/szybciej” itp.). Nie tylko skraca to czas testów i uruchomienia rozwiązania, ale również zwiększa zaufanie do oferowanej technologii i całego procesu inwestycji.
Dowiedz się więcej
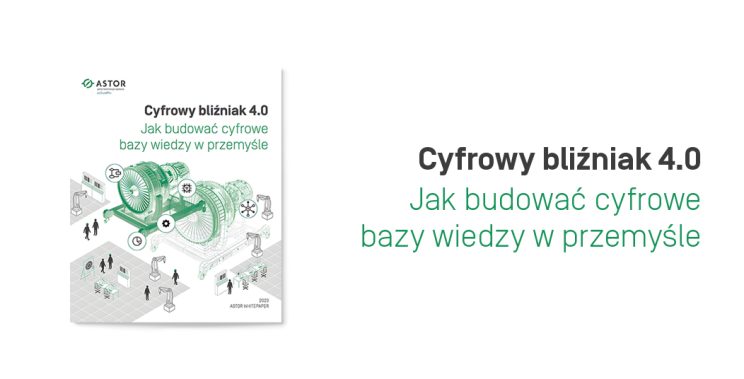
Dowiedz się więcej o cyfrowym bliźniaku w nowej publikacji „Cyfrowy bliźniak 4.0. Jak budować cyfrowe bazy wiedzy w przemyśle.„