Testuj zanim wykorzystasz w procesie produkcyjnym – kooperacja przemysłu z Uniwersytetem Rolniczym w Krakowie
Stanowisko umożliwia firmom produkcyjnym prowadzenie rozmaitych testów, np. sprawdzenie jakiego rodzaju chwytaki są optymalne do określonego rodzaju produktów, testowanie schematów paletyzacji, praktyczne ustalenie jak powinno wglądać i z jakich komponentów się składać stanowisko do paletyzacji.
Poniżej publikujemy artykuł, który pierwotnie ukazał się „Biuletynie Automatyki”, wyjaśniający techniczne aspekty tego rozwiązania, ale też korzyści jakie z jego wykorzystania mogą odnieść firmy produkcyjne.
Centrum Innowacji oraz Badań Prozdrowotnej i Bezpiecznej Żywności jest jednostką Uniwersytetu Rolniczego w Krakowie, której celem jest wspieranie środowiska naukowego oraz firm z branży spożywczej, poprzez kompleksowe podejście do badań w zakresie produkcji żywności. Przedmiotem badań jest całość procesu wytwarzania – począwszy od analizy surowców, poprzez zaprojektowanie nowego produktu lub procesu produkcyjnego w laboratoriach, uruchomienie produkcji i analizę efektów, aż po optymalizację warunków przechowywania produktów i gospodarkę odpadami.
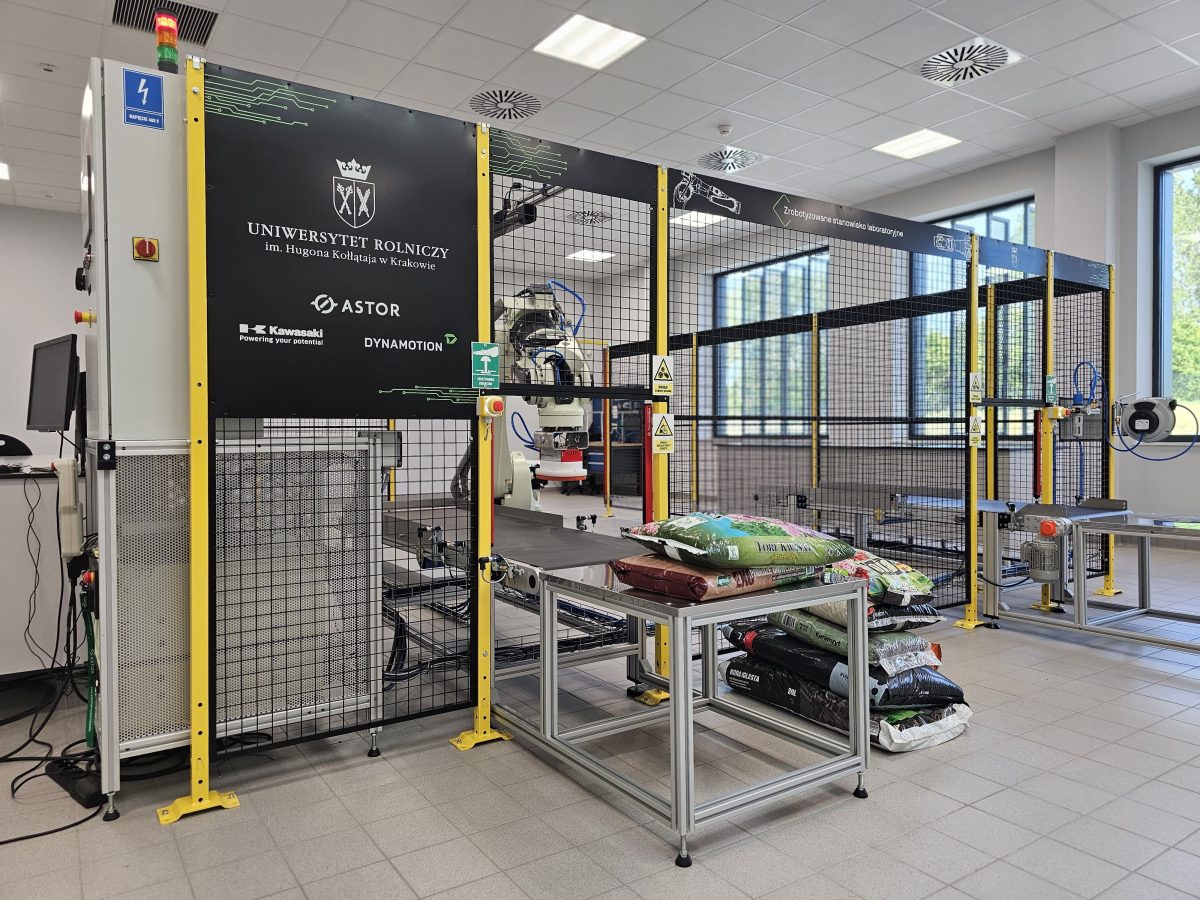
W skład Centrum Innowacji oraz Badań Prozdrowotnej i Bezpiecznej Żywności wchodzi szereg nowoczesnych pracowni specjalistycznych, w tym:
- pracownie technologiczne: piekarsko-ciastkarska, technologii mięsa i ryb, minibrowar ze śrutownią, pracownia sensoryczna,
- laboratoria: mikrobiologii żywności i bezpieczeństwa mikrobiologicznego, analityczne, HPLC MS-MS, technologii przetwarzania odpadów,
- pracownia procesów podstawowych, wyposażona m.in. w ekstruder dwuślimakowy wraz z przystawką teksturującą do białek, ekstraktor CO2 w stanie nadkrytycznym, suszarkę rozpyłową, wyparkę próżniową, liofilizator, maszynę wielozadaniową, urządzenie do utrwalania żywności metodą wysokich ciśnień.
Centrum Innowacji oraz Badań Prozdrowotnej i Bezpiecznej Żywności dysponuje również specjalistycznymi laboratoriami, umożliwiającymi współpracę naukową z innymi ośrodkami akademickimi i badawczymi. W ich skład wchodzą między innymi laboratorium wysokospecjalistycznych technik analitycznych (wyposażone w analizator zapachów), technologii soków, napojów i win, technologii przetwórstwa mleka, pracownia gastronomiczna, pracownia bioprocesów, laboratorium fizycznych modyfikacji (wyposażone w stanowiska do utrwalania żywności dzięki pulsacyjnego pola elektrycznego oraz promieniowania elektromagnetycznego), laboratorium suszarnicze i odzyskania substancji prozdrowotnych oraz laboratorium sortowania, konfekcjonowania, pakowania i znakowania surowców.
Laboratorium sortowania, konfekcjonowania, pakowania i znakowania surowców
Rolnictwo wraz z przemysłem spożywczym stanowią jedne z najważniejszych i najszybciej rozwijających się dziedzin polskiej gospodarki. Udział branży rolno-spożywczej w 2019 r. w całkowitej wartości produkcji sprzedanej przemysłu był znaczący i wyniósł blisko 17% (Przemysł rolno-spożywczy w Polsce, 2024). Przedsiębiorstwa tej branży, aby pozostać konkurencyjnymi i utrzymać pozycję na rynku, muszą inwestować w innowacyjne techniki i technologie, do których należy zaliczyć automatyzację i robotyzację, wspierane przez systemy detekcji, sortowania, konfekcjonowania i pakowania produktów rolno-spożywczych. Wdrożenie nowoczesnych systemów technicznych, a przez to ograniczenie ingerencji człowieka w proces produkcyjny, pozwala na poprawę bezpieczeństwa pracy, obniżenie kosztów oraz zwiększenie wydajności i elastyczności produkcji. Istotna jest również możliwość uzyskania i dotrzymania wysokich standardów jakościowych, trudnych do osiągnięcia przy wykorzystaniu tradycyjnych metod produkcji.
Świadomość złożoności zagadnień towarzyszących implementacji nowoczesnych technik i technologii w branży rolno-spożywczej przyczyniła się do powstania w Centrum Innowacji oraz Badań Prozdrowotnej i Bezpiecznej Żywności laboratorium sortowania, konfekcjonowania, pakowania i znakowania surowców. Aktywność tej jednostki skupiać się będzie na zapewnieniu wsparcia przedsiębiorcom sektora rolno-spożywczego poprzez dostarczenie rozwiązań z zakresu zrobotyzowanych linii technologicznych. Laboratorium oferuje im możliwość przetestowania wstępnych koncepcji projektów, związanych z procesem pakowania i paletyzacji. Czynnikiem utrudniającym realizację procesu zrobotyzowanego pakowania jest, występująca głównie w przemyśle rolno-spożywczym, duża różnorodność cech produktów. Należy tu wymienić zmienność takich własności jak: masa, kształt, wymiary geometryczne, adekwatności powierzchni miejsc uchwycenia, sztywność, podatność na naprężenia zewnętrzne, a także wrażliwość na uszkodzenia.
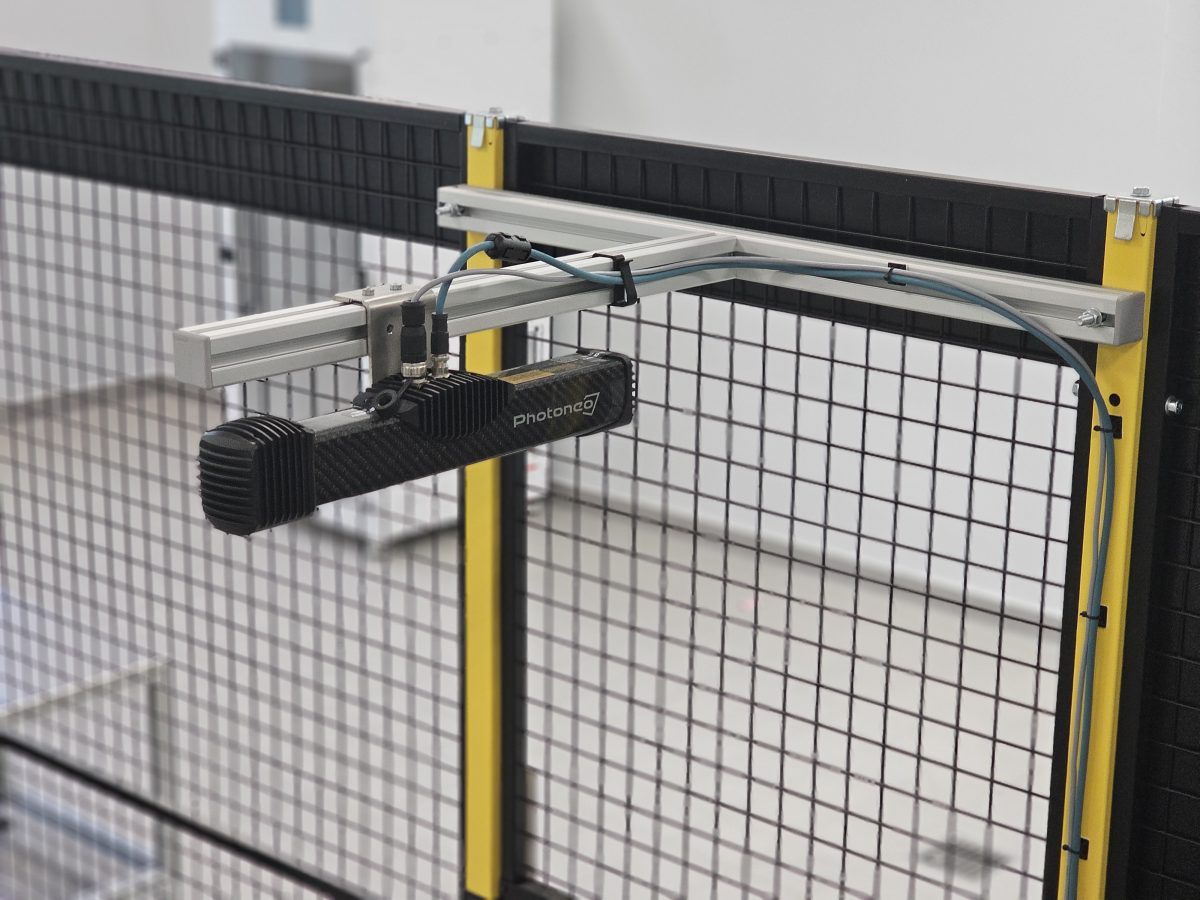
Głównym elementem laboratorium jest system składający się z robota Kawasaki Robotics, zintegrowanego z zaawansowanym układem wizyjnym Photoneo 3D Vision. kooperacja pomiędzy robotem a układem wizyjnym pozwala na precyzyjne monitorowanie i analizowanie procesów produkcyjnych, co przekłada się na efektywną reakcję na wszelkie zmiany w środowisku produkcyjnym. Takie podejście zapewnia systemowi elastyczność, umożliwiającą dostosowanie do zmieniających się warunków produkcji, zwłaszcza w kontekście dynamicznych zmian asortymentu produkowanych towarów. Laboratorium ma być nie tylko przestrzenią testowania nowatorskich rozwiązań, ale także miejscem wymiany doświadczeń i know-how pomiędzy przedsiębiorcami. Dzięki laboratorium przedsiębiorcy z branży rolno-spożywczej zyskają nie tylko dostęp do zaawansowanej technologii, ale także możliwość budowania silnej wspólnoty, która sprzyja wzajemnej inspiracji i rozwojowi. W rezultacie laboratorium nie tylko będzie odpowiadać na bieżące potrzeby przedsiębiorców, ale także stanie się źródłem innowacyjnych rozwiązań, które mają potencjał odmienić oblicze branży rolno-spożywczej.
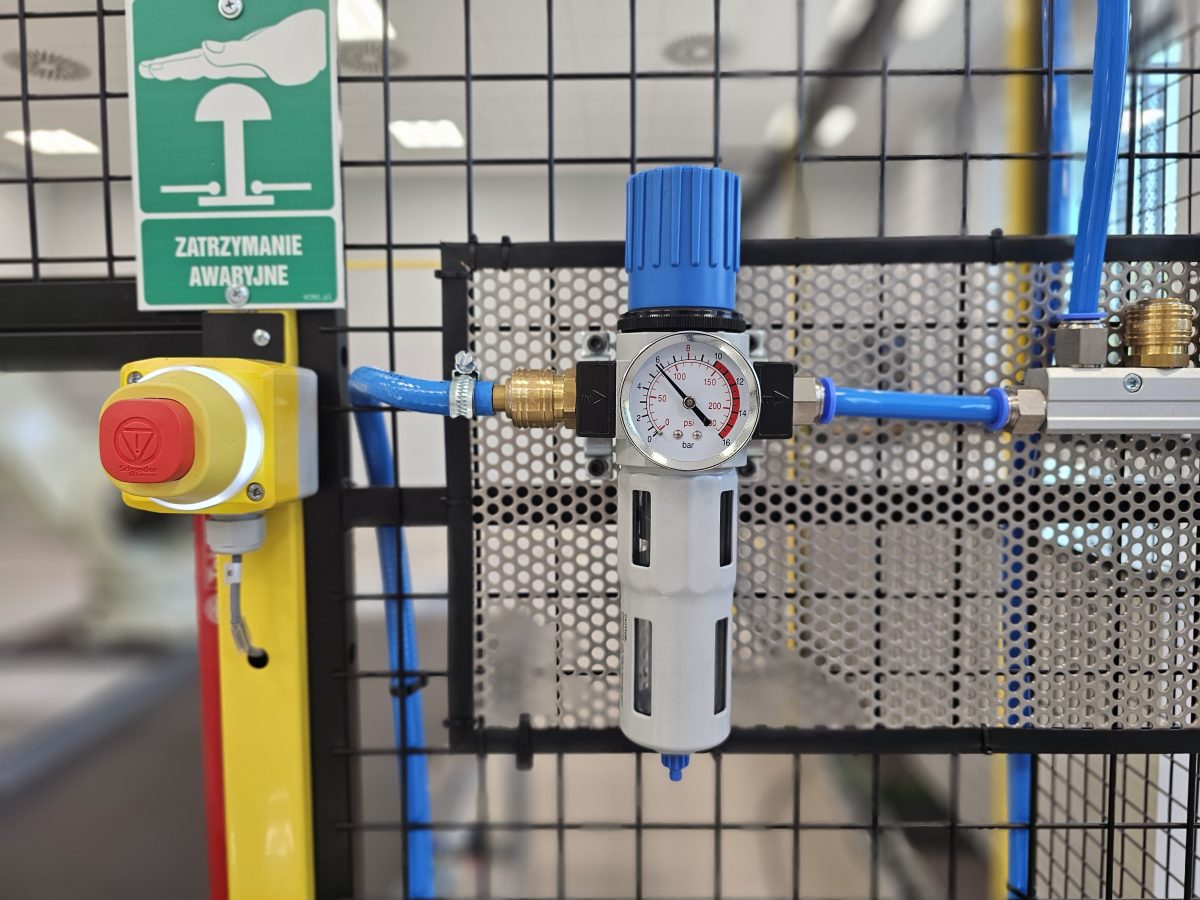
Stanowisko badawcze z robotem paletyzującym Kawasaki Robotics
Głównym elementem stanowiska jest robot BX100L firmy Kawasaki Robotics, wyposażony w chwytak podciśnieniowy firmy Piab. Współpracuje on z systemem wizyjnym Photoneo Vision 3D, który wykorzystuje techniki sztucznej inteligencji: sieci neuronowe oraz uczenie maszynowe. Za bezpieczeństwo stanowiska odpowiadają urządzenia Telemecanique Sensors. W standardowej konfiguracji stanowiska badawczego worki podawane są na taśmę wejściową. Każdy worek poruszający się na taśmie jest poddawany analizie przez system wizyjny, który w pierwszym rzędzie rozpoznaje, czy obiekt znajdujący się na taśmie faktycznie jest workiem. Jest to możliwe dzięki algorytmom sztucznej inteligencji, które zostały „nauczone” definicji worka. o ile na taśmę trafi obiekt, który nie zostanie rozpoznany, stanowisko zatrzymuje się. Rola systemu wizyjnego nie kończy się na samym rozpoznaniu worka. W następnej kolejności wykonywane są zdjęcia oraz skanowany jest dokładny kształt i umiejscowienie worka na taśmie. Na podstawie tych zdjęć oraz zeskanowanej chmury punktów system Photoneo wyznacza miejsce, w którym powinien zostać przyłożony chwytak, a także dokładną orientację chwytaka, która będzie optymalna, tak aby worek został jak najlepiej uchwycony.
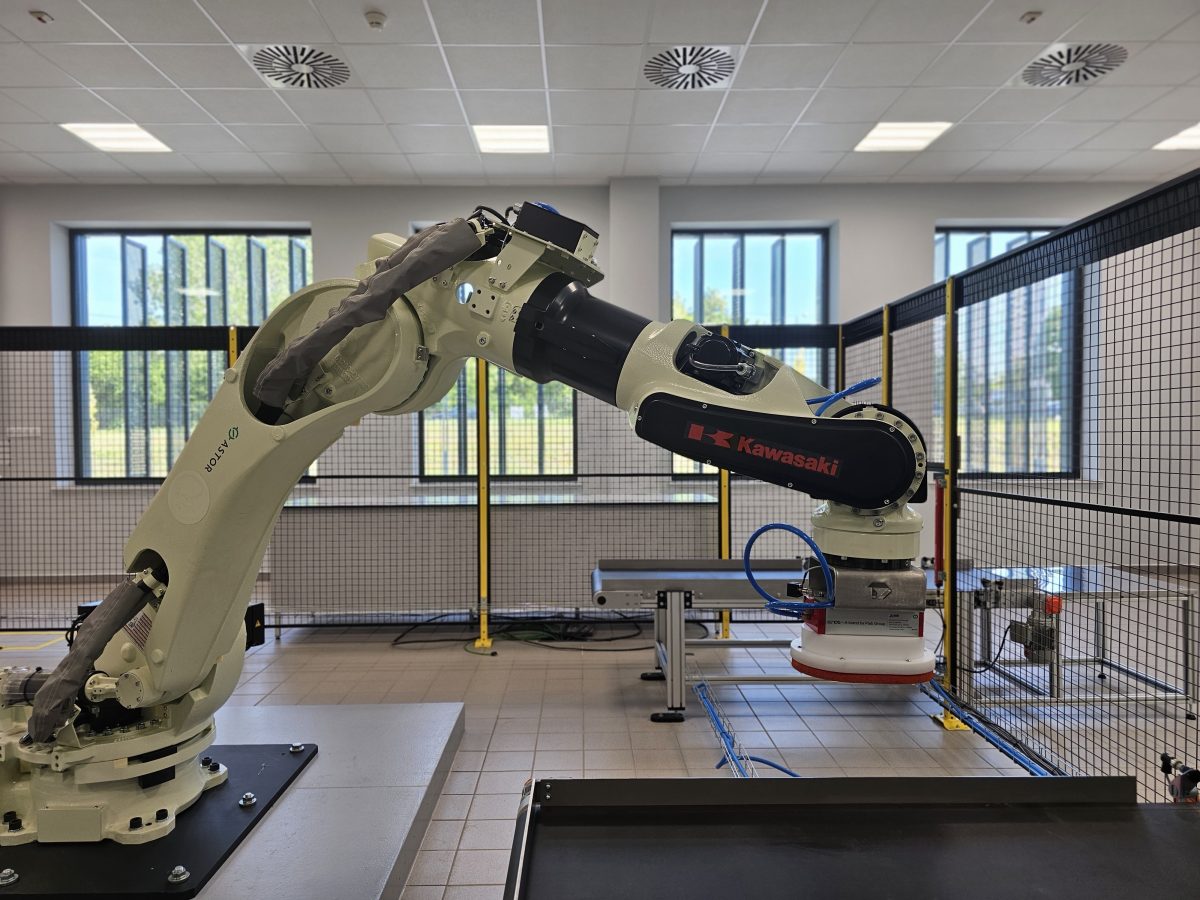
Innymi słowy system wizyjny weryfikuje, jaki worek porusza się po taśmie, jak gwałtownie się porusza, jak dokładnie wygląda – i jak należy go chwycić, aby zapewnić optymalne pobranie. W opisywanym rozwiązaniu program robota nie jest zdefiniowany w sposób sztywny, gdyż punkt pobrania, a przez to trajektoria dojazdu robota do worka, jest każdorazowo wyliczana przez system Photoneo. Należy przy tym podkreślić, iż cała operacja odbywa się w czasie ruchu worka po taśmie, bez konieczności jej zatrzymania. Zastosowanie systemu wizyjnego Photoneo zapewnia nie tylko maksymalną wydajność procesu, ale również niezwykłą uniwersalność stanowiska. Nie wymaga ono rekonfiguracji ani przeprogramowywania przy zmianie asortymentu worków. Prawidłowo nauczony algorytm rozpozna każdy worek, niezależnie od koloru czy rozmiaru. W warunkach dużej zmienności parametrów utrudniających uchwycenie worka, zadawalającą efektywność procesu pakowania pozwala uzyskać zastosowanie chwytaka o specjalnej konstrukcji, umożliwiającej dostosowanie parametrów związanych z uchwyceniem i czynnościami manipulacyjnymi do indywidualnych cech pakowanych produktów. W opisywanym stanowisku robot Kawasaki Robotics wyposażony został w chwytak podciśnieniowy firmy Piab. Jest to najłatwiejsze i najefektywniejsze rozwiązanie do pobierania worków.
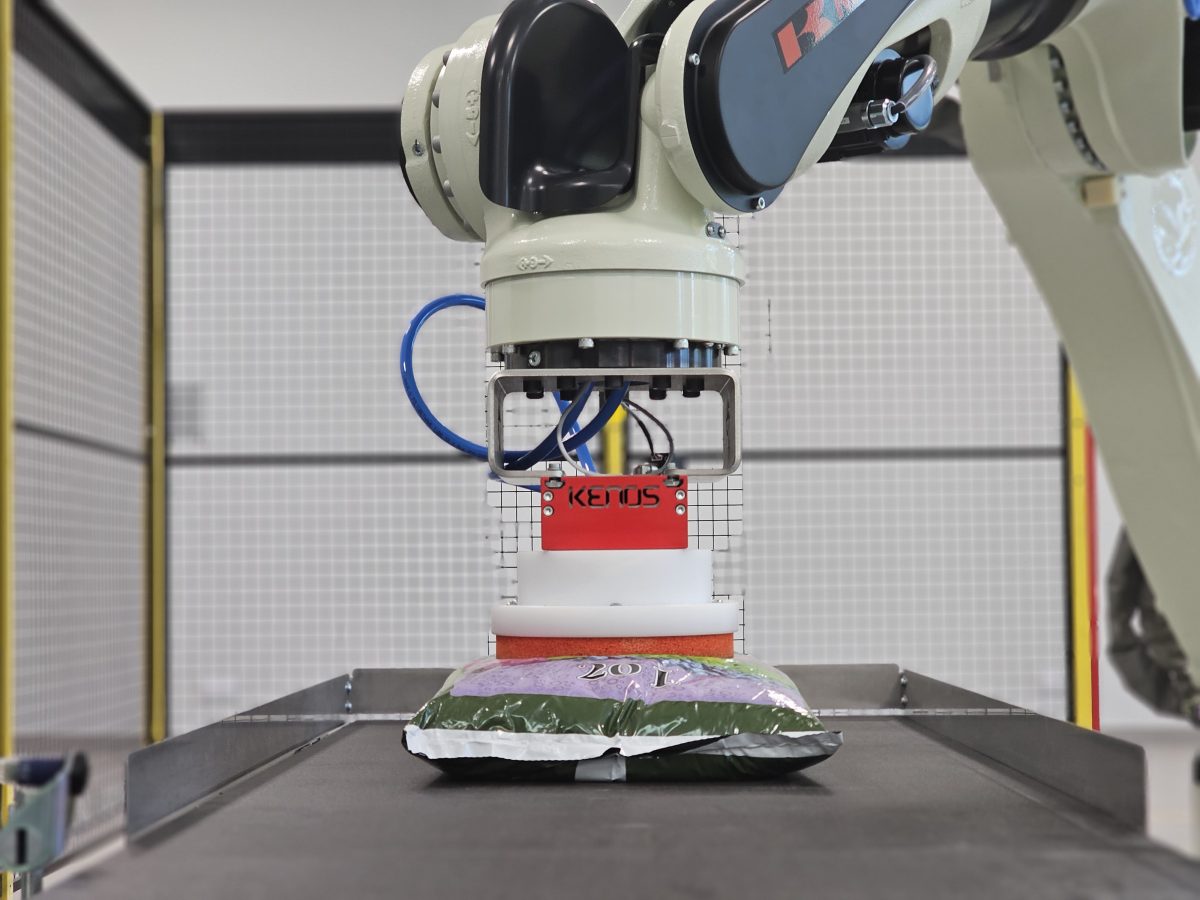
Chwytak jest prosty w obsłudze i uniwersalny – posiada szeroki zakres gabarytów pobieranych worków. Może współpracować z przenośnikiem taśmowym i pobierać worki w ruchu. Alternatywa w postaci chwytaka mechanicznego wymaga dostosowania konstrukcji urządzenia do konkretnego rodzaju worków, a także wymusza zatrzymanie transportu worka przed jego pobraniem. Dodatkową zaletą zastosowanego chwytaka jest możliwość jego przekonfigurowania w taki sposób, aby mógł przenosić kartony.
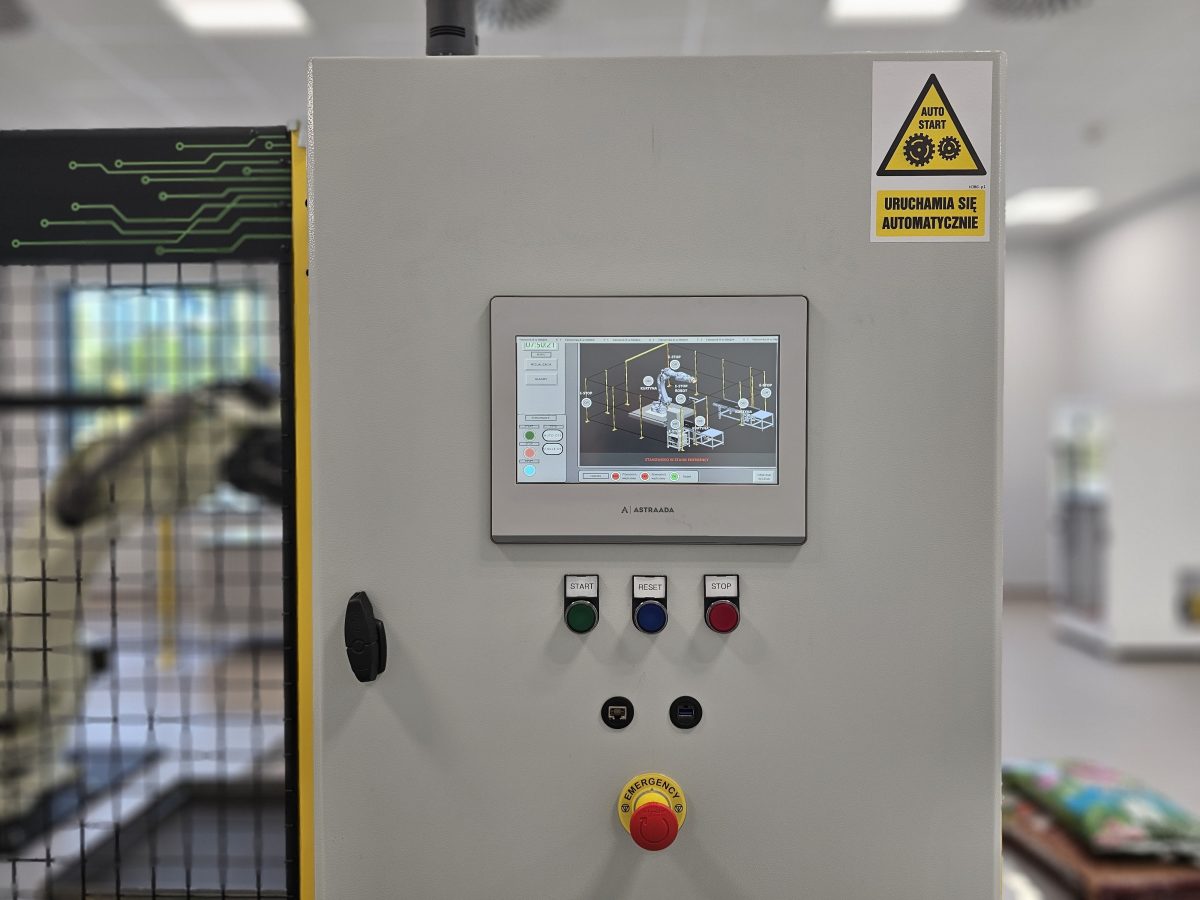
Systemy bezpieczeństwa
Opisywane stanowisko ma charakter uniwersalny, dlatego zastosowane zostały w nim różnorodne systemy bezpieczeństwa. Są to systemy bierne, takie jak wygrodzenie mechaniczne, chroniące przestrzeń pracy robota, a także aktywne systemy bezpieczeństwa firmy Telemecanique Sensors, m.in. kurtyny świetlne, chroniące otwory technologiczne i dostępowe do stanowiska. W przypadku kurtyn zachowana została strefa dobiegu, a dodatkowym uzupełnieniem jest system bezpieczeństwa Cubic-S, charakterystyczny dla robotów Kawasaki Robotics. Umożliwia on dodatkowe zabezpieczenie obszaru pracy robota w sposób wirtualny. Wystarczy programowo zdefiniować, jaka przestrzeń pracy jest dozwolona, a każdorazowe wyjście robota poza tę przestrzeń spowoduje zatrzymanie urządzenia. Część kurtyn bezpieczeństwa w połączeniu z dodatkowymi czujnikami realizuje funkcję mutingu, która umożliwia podanie do zabezpieczonego obszaru wybranych obiektów. Dodatkowe czujniki rozpoznają, czy obiekt który przeciął kurtynę to worek i w zależności od tego uruchamiają alarm lub nie. Tego rodzaju kurtyna została zastosowana w taśmie wejściowej dla worków. Prawidłowo podany worek może przejść przez kurtynę, natomiast o ile znajdzie się w tym miejscu inny obiekt (np. ręka operatora), system zostanie awaryjnie zatrzymany. Zastosowanie wielu różnych zabezpieczeń sprawiło, iż możliwe jest testowanie różnych aplikacji i konfiguracji stanowiska. Dzięki zachowaniu otwartego dostępu do stanowiska mogą, np. we właściwym momencie cyklu, wjechać roboty autonomiczne, dostarczające lub odbierające palety.
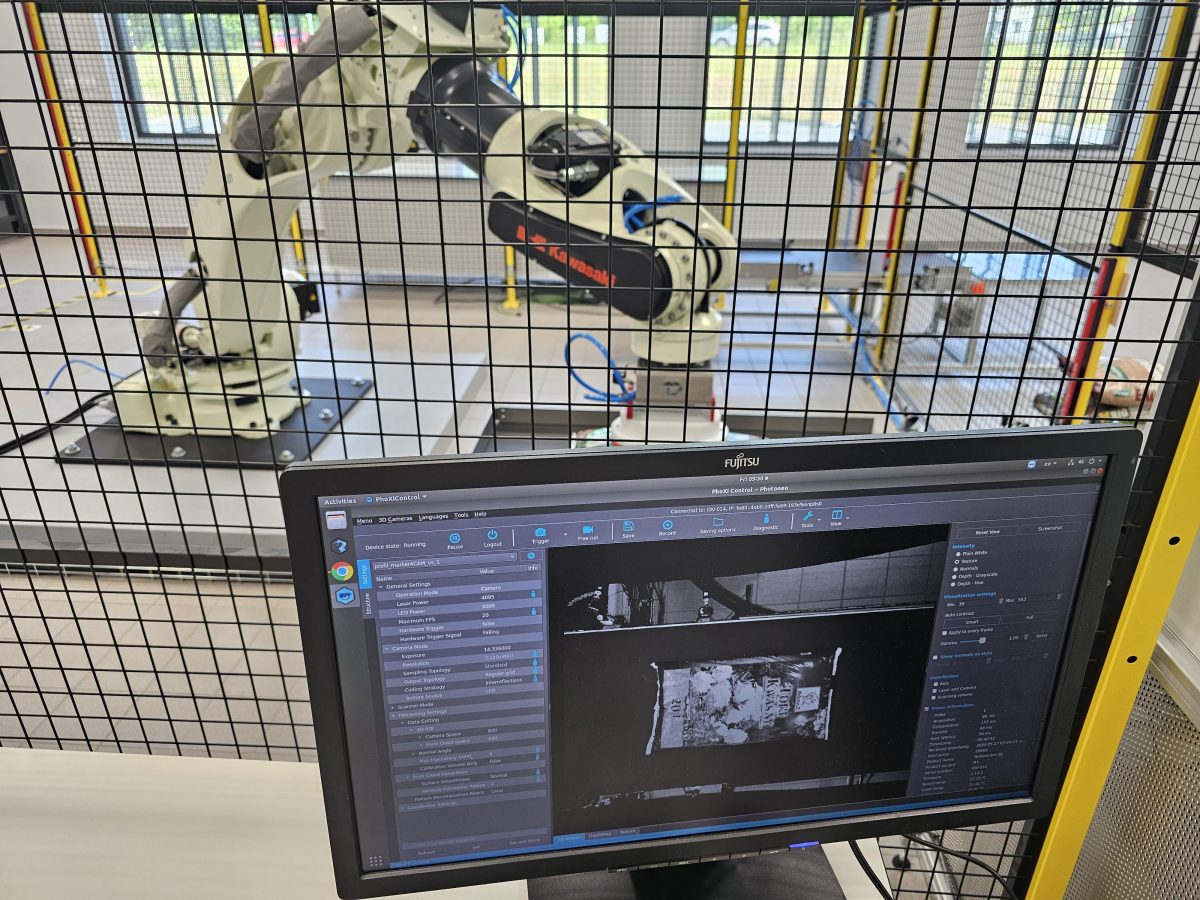
Co można zweryfikować na stanowisku badawczym?
Opisywane stanowisko umożliwia przeprowadzenie testów i badań, które pomogą zweryfikować w praktyce koncepcje przeznaczone do wdrożenia w realiach przemysłowych. Producenci żywności, dostarczający swoje produkty w workach, mogą dzięki niemu uzyskać trzy istotne korzyści.
1. Sprawdzenie, czy określone produkty mogą być pobierane tego typu chwytakami. Stanowisko umożliwia weryfikację, czy chwytak podciśnieniowy prawidłowo pobierze konkretny worek. A o ile tak, to jak on będzie się zachowywał podczas przenoszenia i układania. Czy folia utrzyma ciśnienie? Jak zachowa się produkt w worku? Czy istnieje ryzyko uszkodzenia produktu? Wszystkie te aspekty mogą być sprawdzone w praktyce, w warunkach laboratoryjnych.
2. Przetestowanie schematów paletyzacji. W podstawowej konfiguracji stanowiska worki są przez robota przekładane na taśmę wyjściową. Ale stanowisko można przekonfigurować, umieszczając w miejscu tej taśmy stację do paletyzacji. Po umieszczeniu w niej palety możliwe jest testowanie paletyzacji worków, w tym także mixing worków na paletach. Pozwala to przekonać się, iż proces jest realny (proof-of-concept). Możliwe jest także zmierzenie czasów cyklu, a także sprawdzenie, jak dynamiczne ruchy mogą być wykonywane bez ryzyka uszkodzenia worków. Dodatkowo, jak wspomniano wyżej, chwytak może być przekonfigurowany do pracy z kartonami, dzięki czemu możliwe jest również testowanie paletyzacji kartonów.
3. Praktyczne sprawdzenie, jak powinno wyglądać stanowisko do paletyzacji. Opisywane wdrożenie pokazuje, jak wygląda całe stanowisko do paletyzacji: ile potrzeba miejsca, jakie elementy są wymagane i jak rozwiązać temat bezpieczeństwa. Można przekonać się, jak wygląda przestrzeń robocza robota, jakie wygrodzenia należy zastosować. Jest to więc gotowy wzorzec, który stanowi realistyczną symulację podobnych lub też większych systemów w przemyśle.
Opisane stanowisko zrealizowane zostało we współpracy z firmami ASTOR i DYNAMOTION. Należy podkreślić, iż jego aktualna konfiguracja nie jest niezmienna. W zależności od potrzeb klienta zgłaszającego się z pomysłem na realizację procesu pakowania możliwe jest przezbrojenie stanowiska (dobór chwytaka, zmiana algorytmu sterowania itd.) w celu przetestowania założeń dowolnej koncepcji.
Współautorem artykułu jest dr inż. Stanisław Lis z Katedry Inżynierii Bioprocesów, Energetyki i Automatyzacji na Wydziale Inżynierii Produkcji i Energetyki na Uniwersytecie Rolniczym w Krakowie.