Poniżej publikujemy artykuł, który pierwotnie ukazał się magazynie „Biuletyn Automatyki”, wyjaśniający techniczne aspekty tego rozwiązania, ale też korzyści jakie z jego wykorzystania mogą odnieść firmy produkcyjne.
Zadaniem poszczególnych Wydziałów AGH jest podejmowanie współpracy z przedstawicielami przemysłu oraz wyjście z ofertą badawczą naprzeciw potrzebom, które w tej chwili kreuje rynek. Jest to rynek dynamiczny, co regulowane jest nie tylko popytem i podażą na produkty oferowane przez przedsiębiorstwa, ale również europejskimi i polskimi ramami prawnymi, w których wszyscy musimy się odnaleźć. Jest to w tej chwili szczególnie odczuwalne dla Wydziału Inżynierii Metali i Informatyki Przemysłowej oraz instytucji z branży przemysłu ciężkiego, skupionego wokół wytwarzania i przetwarzania metali, a także przemysłu energochłonnego, co w świetle wszechobecnej dyskusji na temat Zielonego Ładu jest wyjątkowo trudne. Pomimo wielu przeciwności natury instytucjonalnej, prawnej czy ekonomicznej, wieloaspektowa kooperacja pomiędzy przemysłem i akademią utrzymuje się i rozwija, do czego obie strony dokładają ciągłych starań.
Nowoczesny przemysł bez nauki nie istnieje, podobnie jak innowacyjna nauka bez przemysłu.
– prodziekan Wydziału IMiIP ds. Nauki i Współpracy, dr hab. inż. Łukasz Rauch, prof. AGH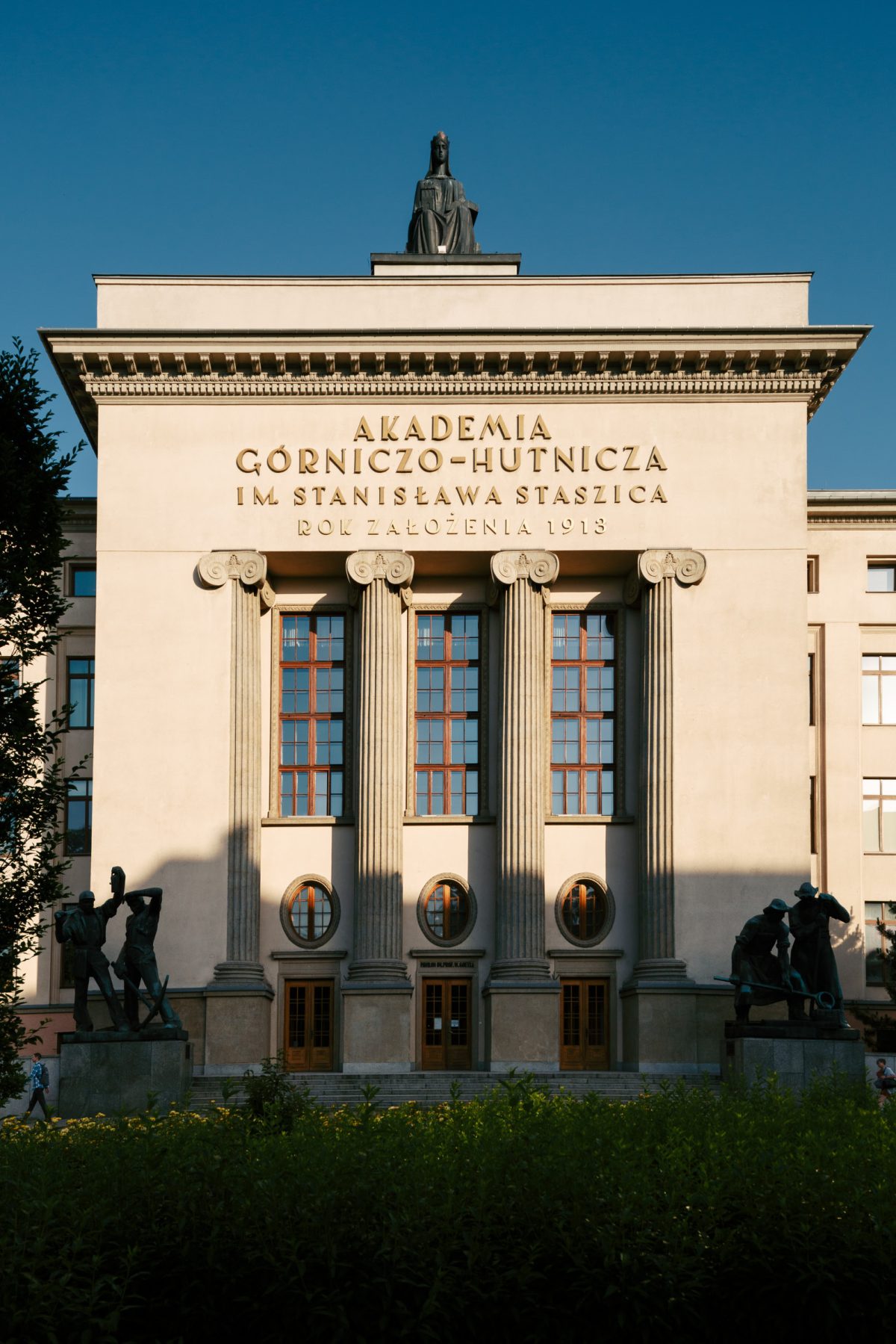
Przykładem są podpisane umowy ramowe, wspólnie organizowane warsztaty, seminaria i konferencje oraz staże i działania skierowane do studentów. Tylko w ostatnich latach AGH podpisała z przedstawicielami przemysłu kilkadziesiąt umów ramowych, projektowych oraz umów o zachowaniu poufności, dzięki którym kolejne projekty bilateralne i konsorcjalne mogły być z powodzeniem realizowane. Przykładem takiej współpracy są również stanowiska badawcze, które nie mogłyby zostać zbudowane bez ścisłej współpracy z przemysłem i zaangażowania funduszy ze strony prywatnych przedsiębiorców.
Zrobotyzowane stanowisko do kucia na gorąco
Zrobotyzowane stanowisko dydaktyczno-badawcze do kucia na gorąco powstało w Katedrze Plastycznej Przeróbki Metali i Metalurgii Ekstrakcyjnej na Wydziale Inżynierii Metali i Informatyki Przemysłowej Akademii Górniczo-Hutniczej w Krakowie. W ramach wydziału prowadzony jest szereg kierunków związanych z metalurgią i inżynierią materiałową, a także z informatyką stosowaną w przemyśle, przede wszystkim ciężkim. Jak podkreśla dr inż. Grzegorz Michta, prodziekan ds. kształcenia i studenckich, wydział kształci bardzo interdyscyplinarnie i praktycznie.
Wykładowcy i pracownicy dydaktyczni dbają o to, aby studenci uzyskiwali nie tylko wiedzę z zakresu wąskiej specjalizacji, ale również poszerzali swoje horyzonty i zdobywali wiele innych kompetencji, w tym miękkich, przydatnych w pracy zawodowej w nowoczesnym przemyśle. Te kompetencje, do których zaliczamy komunikację, organizację, samodzielność, ale jednocześnie umiejętność pracy w zespole, analityczne myślenie, kreatywność i empatię. Równie ważne są umiejętności słuchania i pracy pod presją czasu, prezentacji, a także obrony własnego zdania. To wszystko, w połączeniu z praktyczną wiedzą, daje komplementarne wykształcenie, za pomocą którego absolwenci powinni odnaleźć się w każdych warunkach pracy. Ważne są także kompetencje technologiczne w zakresie pracy z różnymi narzędziami i programami komputerowymi oraz sprawne przyswajanie nowej wiedzy, co w zmieniającej się gwałtownie rzeczywistości jest kluczowe.
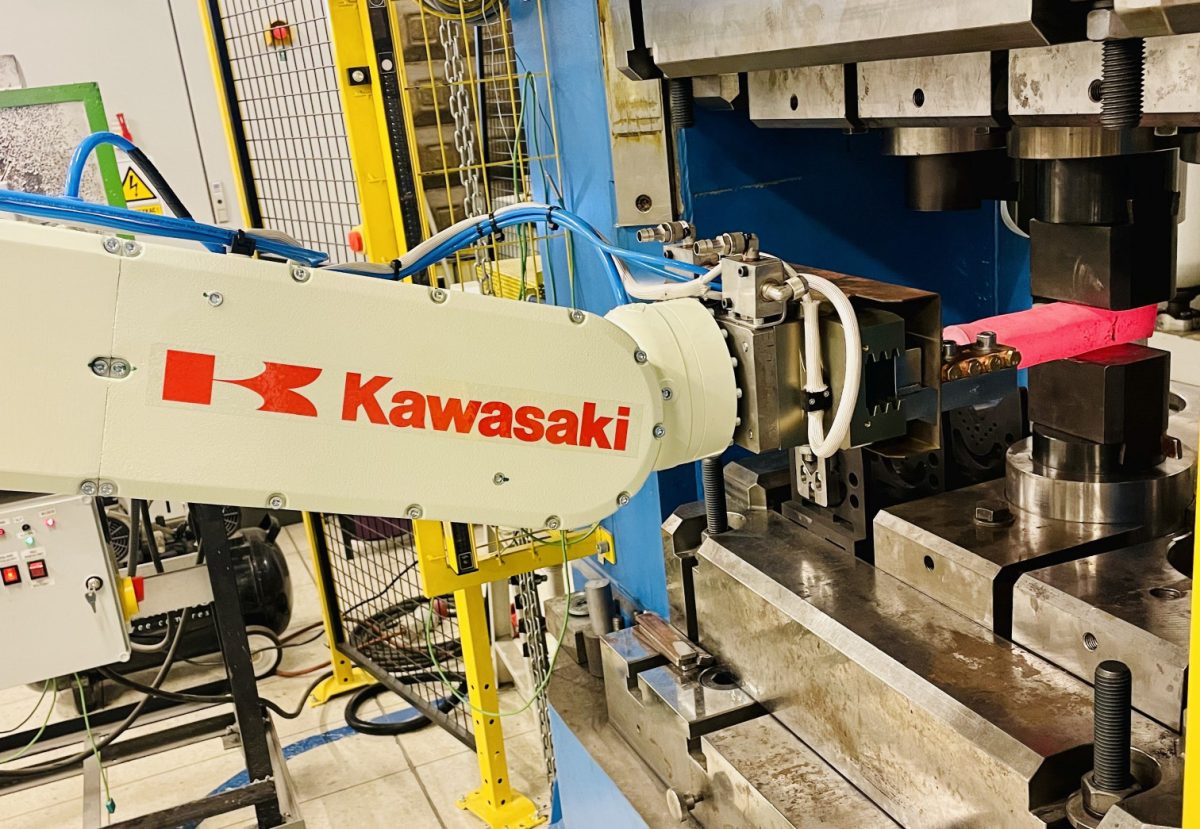
Na Wydziale Inżynierii Metali i Informatyki Przemysłowej kształcenie odbywa się na pięciu kierunkach studiów: dwóch informatycznych, dwóch materiałowych i jednym łączącym wiedzę informatyczną, edukacyjną i materiałową. Na kierunku Informatyka Techniczna i Inżynieria Obliczeniowa studenci, obok bardzo dobrego przygotowania informatycznego, mają możliwość zapoznania się z procesami technologicznymi, dla których tworzą różnego typu rozwiązania informatyczne. Dlatego nasi studenci, obok bardzo dobrego przygotowania informatycznego, mają wiedzę technologiczną i znają systemy przemysłowe, dla których tworzą różnego typu rozwiązania informatyczne (systemy zarządzania, cyfrowe bliźniaki, systemy wirtualnej i rozszerzonej rzeczywistości, systemy dla BigData i rozwiązania chmurowe).
Na kierunku Inżynieria Metali studenci zdobywają wiedzę branżową, związaną z adekwatnościami i technikami otrzymywania materiałów metalicznych i niemetalicznych, kompozytowych, biomateriałów, materiałów funkcjonalnych oraz materiałów o ściśle zdefiniowanych adekwatnościach i zastosowaniach. Inżynieria Procesów Produkcyjnych to unikatowy kierunek, związany z przetwórstwem metali i stopów, recyklingiem metali i utylizacją odpadów technologicznych techniki cieplnej (gospodarka w obiegu zamkniętym), podstawami automatyki przemysłowej (Przemysł 4.0), ekologią i ochroną środowiska, modelowaniem i komputerowym wspomaganiem prac inżynierskich oraz drukiem 3D wyrobów metalowych. Kierunki materiałowe w swoich programach studiów mają dużą ilość przedmiotów informatycznych, w tym związanych z symulacjami różnych procesów, tak potrzebnych współczesnemu inżynierowi. Kolejny kierunek to Edukacja Techniczno-Informatyczna. Jest to kierunek łączący informatykę z ogólnie pojętym materiałoznawstwem, co daje możliwości pracy w branży szkoleniowej, w obszarze wdrażania systemów czy zarządzania projektami (informatycznymi i technologicznymi). Wiedząc, iż rozwój technologiczny zależy od harmonijnego współdziałania branży IT i przemysłowej, programy studiów, niezależnie od kierunku, są tak konstruowane, aby te dwie branże przenikały się nawzajem, co sprawia, iż nauczanie jest interdyscyplinarne i komplementarne.
Przykładem realizacji tej misji jest nowoczesne, zrobotyzowane stanowisko do kucia na gorąco, które zostało uruchomione w 2023 roku. Na stanowisku tym tradycyjny proces przeróbki plastycznej metalu dzięki prasy hydraulicznej został rozbudowany o robota przemysłowego, zastępującego operatora w wykonywaniu najtrudniejszych i najbardziej niebezpiecznych zadań.
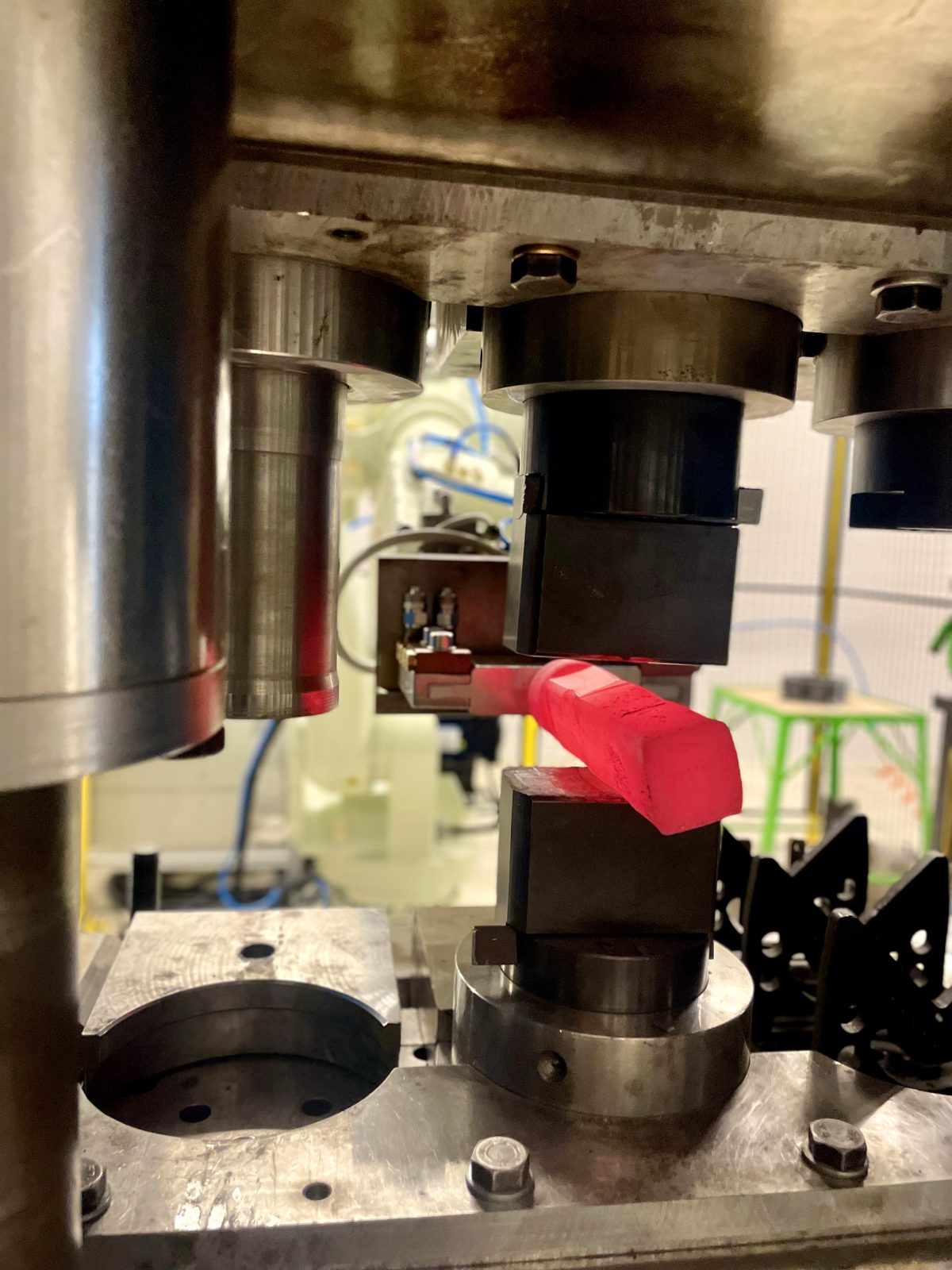
Opis stanowiska
Stanowisko składa się z trzech głównych elementów:
- prasy hydraulicznej,
- pieca elektrycznego,
- robota Kawasaki Robotics RS030N wraz z osprzętem.
Centralnym punktem stanowiska jest prasa hydrauliczna o maksymalnej sile nacisku 500 ton, realizująca operacje kucia na gorąco. Umożliwia ona wykonywanie zarówno kucia swobodnego (wielooperacyjne kształtowanie w narzędziach płaskich, gdzie poszczególne naciski są oddzielane przesunięciami i obrotami kutego elementu), jak i matrycowego (element jest umieszczany w matrycy, która nadaje wykuwanemu przedmiotowi kształt). Przedmiot ten jest wcześniej rozgrzewany w piecu elektrycznym do wymaganej temperatury, sięgającej choćby 1250°C. W tradycyjnym procesie kucia swobodnego przedmiot jest trzymany dzięki specjalnych kleszczy przez operatora, który umieszcza go w przestrzeni roboczej prasy, a następnie odpowiednio nim manipuluje, aby uzyskać wymagany kształt.
W opisywanym stanowisku operator został zastąpiony przez robota przemysłowego Kawasaki Robotics, wyposażonego w specjalistyczny, chłodzony wodą i powietrzem, uchwyt do pracy na gorąco. Robot chwyta rozgrzany w piecu element i umieszcza go w ściśle określonej pozycji w przestrzeni roboczej prasy, gdzie jest on odpowiednio kształtowany. Po każdym nacisku robot przesuwa i obraca kształtowany element w taki sposób, aby wykonać zaprojektowaną sekwencję kucia, pozwalającą na uzyskanie wymaganego kształtu wyrobu. Kawasaki Robotics RS030N manipuluje elementem w taki sposób, aby kucie było wykonane o wiele bardziej precyzyjnie i powtarzalnie, niż zrobiłby to choćby najbardziej wprawny operator.
System bezpieczeństwa
Ważnym elementem stanowiska jest również system bezpieczeństwa. Robot pracuje wewnątrz wygrodzenia zabezpieczającego przed dostaniem się do środka osób niepowołanych. Całością systemu bezpieczeństwa zarządza przekaźnik bezpieczeństwa z serii Preventa XPS Universal. Do niego podłączone są wszystkie urządzenia peryferyjne, takie jak:
- rygle bezpieczeństwa – zabezpieczające drzwi przed otwarciem w trakcie pracy robota w trybie automatycznym,
- przyciski zatrzymania awaryjnego – umieszczone na zewnątrz i wewnątrz stanowiska – pozwalające operatorowi na zatrzymanie pracy robota, gdy zaobserwuje sytuację niebezpieczną.
- krańcówki i kurtyny bezpieczeństwa – zatrzymujące pracę robota w momencie, gdy zostanie przekroczona strefa niebezpieczna lub otwarta osłona.
Prasa hydrauliczna o maksymalnej sile nacisku 500 ton, obsługiwana przez robota trzymającego w szczękach chwytaka 10-kilogramowy detal, rozgrzany do 1200 stopni Celsjusza to stanowisko niosące spore ryzyko dla operatora – dlatego tak ważne jest zastosowanie odpowiedniej ochrony, z wykorzystaniem najwyższej jakości elementów. Dzięki zastosowaniu urządzeń bezpieczeństwa maszynowego od Telemecanique Sensor stanowisko zostało zabezpieczone sprawdzonym i pewnym układem – gwarantującym użytkownikom bezpieczeństwo.
Zastosowanie stanowiska w dydaktyce
Współczesny przemysł chętnie zatrudnia absolwentów, którzy nie są zamknięci w ramach wąskiej specjalizacji, ale posiadają interdyscyplinarne kompetencje, poparte praktycznym doświadczeniem. W przypadku specjalistów od obróbki metali takim dodatkowym, cennym zasobem może być praktyczna znajomość podstaw robotyki, zastosowań robotów przemysłowych, a także umiejętność ich obsługi. Studenci Wydziału Inżynierii Metali i Informatyki Przemysłowej AGH w ramach zajęć prowadzonych na stanowisku poznają nie tylko proces kucia na gorąco, ale także możliwości, jakie daje zastosowanie robota przemysłowego w tego rodzaju aplikacji. Mają możliwość zdobycia wiedzy z zakresu instalowania, podłączania i programowania robota przemysłowego. Mogą w praktyce poznać wszystkie elementy stanowiska zrobotyzowanego, w tym systemy zabezpieczeń i budowę osprzętu dodatkowego, takiego jak np. chwytak. Zdobywają dzięki temu interdyscyplinarną wiedzę, bardzo cenioną na rynku pracy.
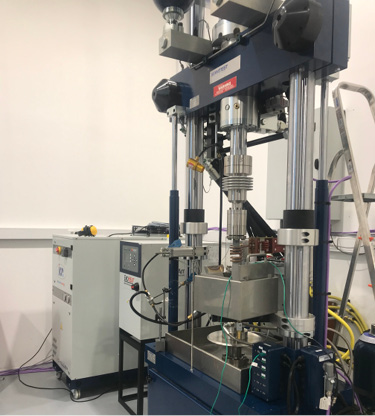
własności materiałów
Zastosowanie stanowiska w badaniach
Stanowisko do kucia na gorąco z robotem Kawasaki Robotics jest również wykorzystywane jako laboratorium testowe i badawcze, którego oferta kierowana jest do przemysłu. Na stanowisku prowadzone są badania, których wyniki umożliwiają optymalizację procesów kucia w komercyjnych kuźniach. W realiach przemysłowych mamy do czynienia z odkuwkami o masie choćby kilkunastu ton. Nie ma możliwości testowania procesu dla tak wielkich elementów, dlatego w Katedrze Plastycznej Przeróbki Metali i Metalurgii Ekstrakcyjnej opracowana została metoda, która pozwala na połączenie symulacji numerycznej procesów przemysłowych z badaniami laboratoryjnymi. Aby taka symulacja dawała wiarygodne wyniki, wykorzystywane są dane zbierane podczas badań przeprowadzanych na dużo mniejszych elementach, wykonanych z takich samych materiałów i odkształcanych w analogicznej sekwencji. Opisywane stanowisko pozwala przeprowadzić szereg eksperymentów i zebrać dokładne dane o tym, jak zachowuje się dany materiał podczas kucia. Możemy zbadać, czy dzieje się coś nieprzewidzianego lub niepożądanego. Możemy też sprawdzić, ile operacji (nacisków prasy) jest konieczne, aby uzyskać adekwatny efekt – zadany kształt lub wydłużenie.
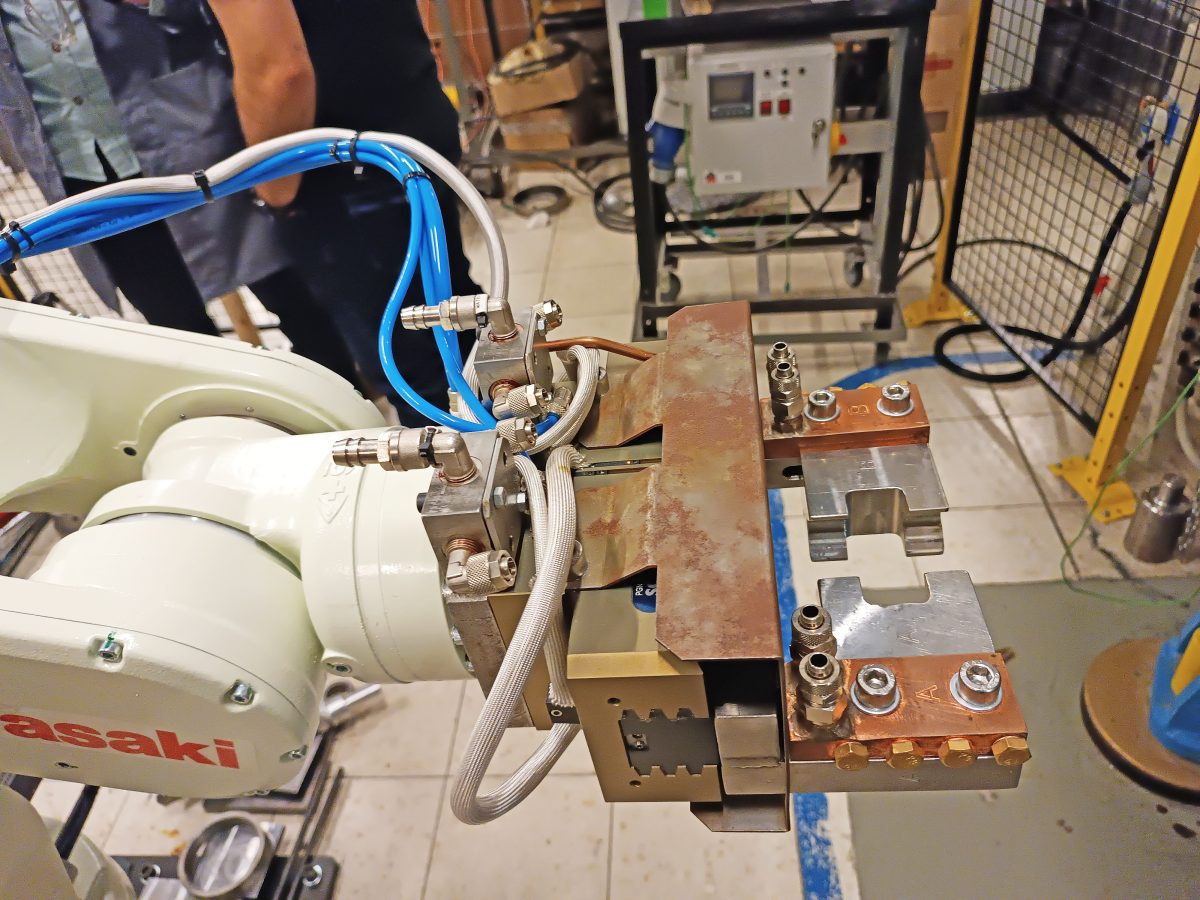
Analizowana jest także zmiana temperatury detalu podczas kucia. Na tej podstawie weryfikowane są parametry wymiany ciepła przyjęte w symulacji numerycznej procesu kucia. Co więcej, z kontrolera robota Kawasaki Robotics można ściągnąć dokładne informacje, związane z aktualnym położeniem robota. Daje to możliwości określenia kierunków płynięcia materiału oraz sił jakie oddziałują na chwytak robota podczas zadawania odkształceń. Wszystkie te dane są następnie wykorzystywane w symulacjach, w ramach których dokonywane jest „przeskalowanie” procesu – z małego przedmiotu testowego w skali laboratoryjnej, na kilkunastotonowy element w skali przemysłowej. Taka symulacja to bezcenne badanie dla przemysłu. Konkretny materiał jest testowany na fizycznym stanowisku, w skali laboratoryjnej. Na tej podstawie przygotowana jest symulacja, która pozwala sprawdzić, jak będzie zachowywał się materiał w skali przemysłowej. Pozwala to skutecznie projektować i optymalizować technologię kucia w realiach przemysłowych oraz badać nowe materiały stosowane na wyroby wykorzystywane w przemyśle energetycznym, wojskowym czy transportowym.
Inne zastosowania
Stanowisko pełni również funkcję demonstracyjną. Dzięki niemu przedstawiciele przemysłowych kuźni mogą przekonać się, w jaki sposób można zintegrować istniejące i pracujące od lat urządzenia kuźnicze z nowoczesną technologią w postaci robotów przemysłowych. Jak wynika z informacji udostępnionych przez branżowe stowarzyszenie Związek Kuźni Polskich, w tej chwili zakłady kuźnicze w Polsce stają przed dylematem związanym z robotyzacją swoich stanowisk. Część zakładów decyduje się na budowę stanowiska od podstaw – zakup maszyny do kucia, pieca, robotów, systemów zabezpieczeń. Inni natomiast modernizują istniejące maszyny i dostosowują stanowisko do kucia z udziałem robota. Można spotkać także rozwiązania, gdzie widoczna jest kooperacja człowiek-robot: operator wykonuje cześć operacji, następnie robot przejmuje detal i podaje go do dalszej obróbki. Dużą trudność i wyzwanie stanowi robotyzacja procesów kucia na młocie. Dynamika procesu i towarzyszące mu drgania są wyzwaniem dla integratorów.
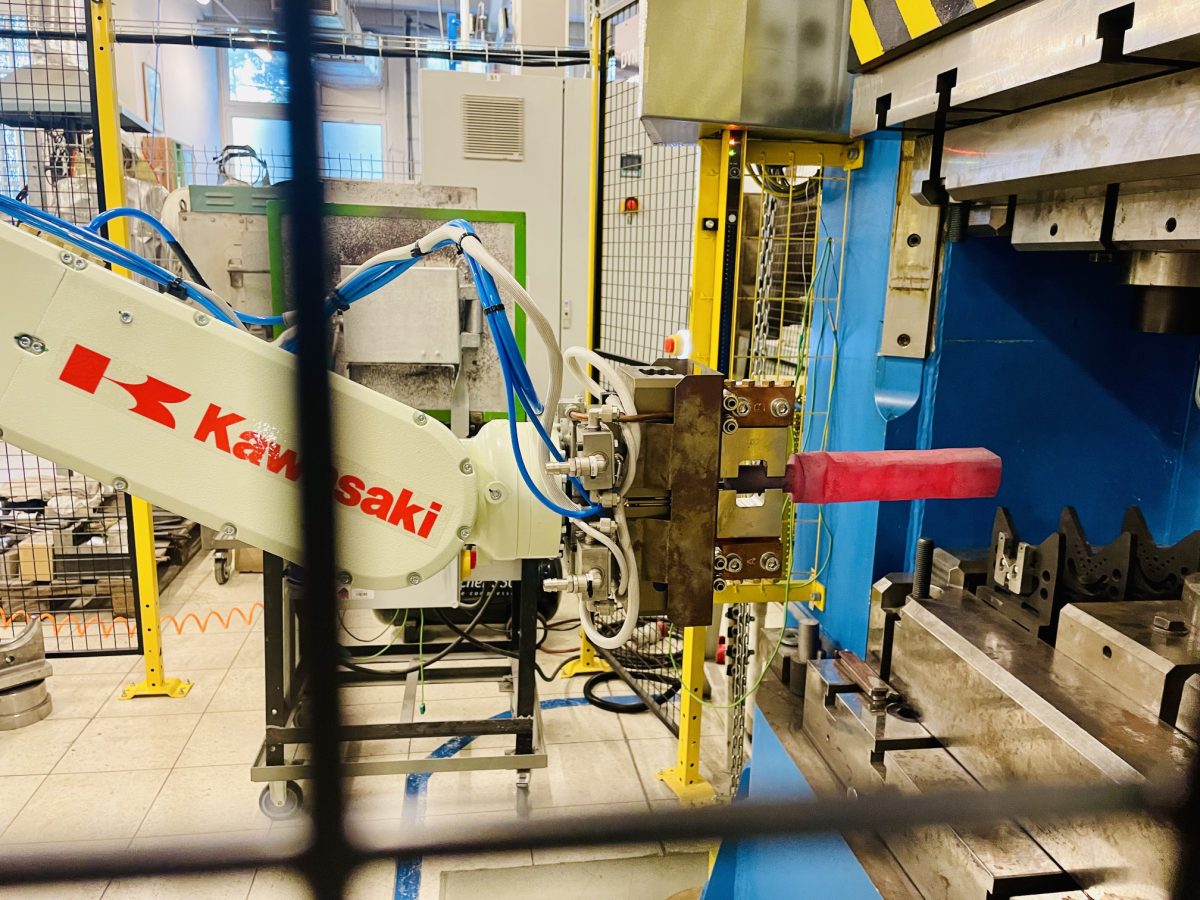
Oprócz robotów bezpośrednio uczestniczących w procesie kucia, w kuźniach jest także miejsce dla robotów transportowych i handlingowych. Transport elementów wsadowych czy gotowych detali niesie ze sobą szereg procedur związanych z logistyką i BHP w zakładzie. Robotyzacja tego typu operacji pozwala na wdrażanie nowych, bezpieczniejszych rozwiązań. Oprócz tego, bezpośrednio po procesie kucia, detale poddawane są obróbce cieplnej oraz mechanicznej. W tym obszarze istnieje szereg możliwości robotyzacji stanowisk. Osobnym zagadnieniem jest regeneracja matryc kuźniczych. Wykonywane w tym celu napawanie polega na naniesieniu materiału na nadmiernie zużyte obszary wykroju matrycy. W celu ograniczenia ilości nanoszonego materiału można wykonać analizę obszarów zużycia (np. przy pomocy skanowania 3D) i precyzyjnie nanieść napawany materiał na konkretne obszary. Wysoka dokładność oraz minimalizacja czasu tej operacji jest możliwa do osiągnięcia dzięki zastosowaniu robota.
Modernizacje kuźni zwykle przebiegają etapowo. Rzadko zdarza się, iż wymieniana jest całość wyposażenia zakładu. Najczęściej te najważniejsze urządzenia – piece i prasy – pozostają na swoim miejscu, poddawane są tylko remontowi lub częściowym modernizacjom. Oznacza to konieczność integracji nowoczesnych urządzeń (sterowników, robotów przemysłowych) z istniejącą technologią, co może wzbudzać wątpliwości i obawy. Przeprowadzając testy na opisywanym stanowisku, możemy przekonać się, w jaki sposób robot przemysłowy współpracuje z prasą, jak przebiega proces i jakie są jego jakościowe efekty. Łatwo zweryfikujemy osiągniętą dokładność, niezawodność całego stanowiska oraz poziom zabezpieczeń. W taki sam sposób można przetestować również drugą konfigurację, czyli aplikację handlingu (przenoszenia elementów). W tej konfiguracji robot pobiera rozgrzany element z pieca, umieszcza go w wykroju matrycy, po czym się wycofuje. Dzięki temu można zademonstrować i przetestować całą procedurę wielooperacyjnego kucia matrycowego, a także niezbędny osprzęt – np. kształt chwytaka czy rozwiązania związane z pozycjonowaniem wyrobu przy pomocy wyrzutników.
Inne stanowiska i plany rozwoju
Projekt opisywanego stanowiska zakłada jego rozbudowę i zaadaptowanie robota do prac dydaktycznych i badawczych, związanych z innymi procesami przeróbki plastycznej metali. w tej chwili realizowane są prace nad uruchomieniem stanowiska do jednopunktowego tłoczenia blach (ang. Single Point Incremental Forming). Zadaniem robota będzie wykonywanie złożonej sekwencji ruchów, pozwalającej na kształtowanie wytłoczek z arkuszy blach przy pomocy niewielkiego narzędzia. Stanowisko będzie wykorzystywane do celów dydaktycznych oraz do badań tłoczności zaawansowanych materiałów dla przemysłu lotniczego.